Coyote machine
Super Member
- Joined
- May 4, 2009
- Messages
- 7,660
- Location
- Southern VT
- Tractor
- 22 SANY SY 50U, '10 Kioti DK 40se/hst KL-401 FEL, loaded tires, KB-2485 bhoe, Tuffline TB160 BB, Woods QA forks, MIE Hydraulic bhoe thumb & ripper tooth, Igland 4001 winch, & GR-20 Log Grapple. Woods BBX72" Brush Mower. Diamondplate aluminum canopy
The following pics are of the second generation of what was originally made for Island Tractor. I asked the manufacturer to add teeth to both the front and backside of the ripper tooth and nicknamed it "The Claw".
The pics are not in any particular order, however they show the claw from different angles and at work ripping out some frozen roots in the bottom group of pics in freezing temps a winter or so ago.
I'm a big fan of using the curl to tear at the roots while lifting up with the serrated edge of the claw to effectively immobilize the root from sliding off the inner curve of the claw. And though it might also be effective to push down and out, as already stated it is an odd maneuver and not easily mastered. So, I prefer to bring the root toward me and up while cutting it/breaking it as the root's natural slipperyness allows or not. Once torn some it is easier to cut further until it submits to hydraulic pressure and gives way completely.
This tooth/ripper is not perfect but it gets the job done, and well at that.
Designed and manufactured by MIE, an approved advertiser on TBN. I have NO affiliation except for having bought numerous of their products over the recent years.
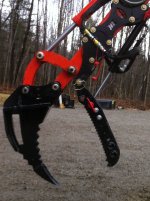
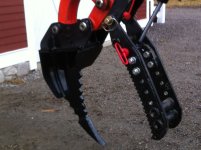
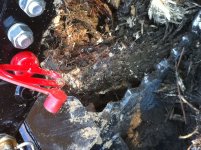
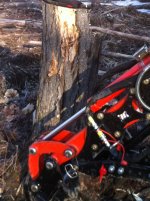
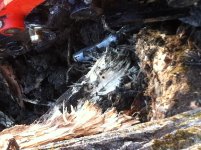
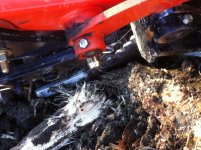
The pics are not in any particular order, however they show the claw from different angles and at work ripping out some frozen roots in the bottom group of pics in freezing temps a winter or so ago.
I'm a big fan of using the curl to tear at the roots while lifting up with the serrated edge of the claw to effectively immobilize the root from sliding off the inner curve of the claw. And though it might also be effective to push down and out, as already stated it is an odd maneuver and not easily mastered. So, I prefer to bring the root toward me and up while cutting it/breaking it as the root's natural slipperyness allows or not. Once torn some it is easier to cut further until it submits to hydraulic pressure and gives way completely.
This tooth/ripper is not perfect but it gets the job done, and well at that.
Designed and manufactured by MIE, an approved advertiser on TBN. I have NO affiliation except for having bought numerous of their products over the recent years.
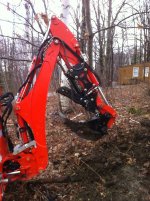
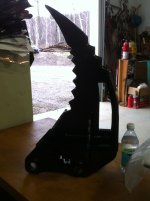
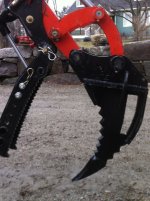
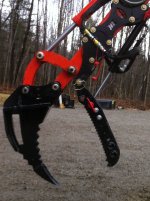
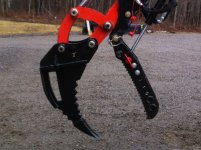
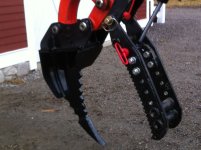
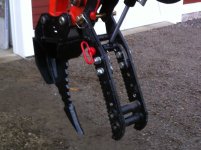
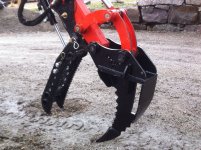
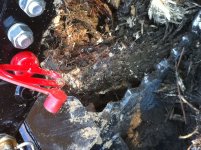
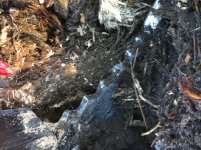
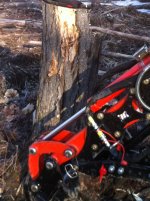
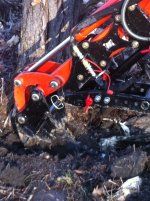
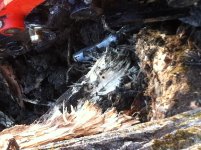
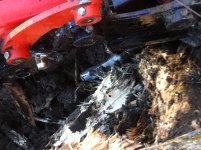
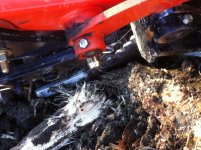