Marcle
Silver Member
- Joined
- Jun 13, 2012
- Messages
- 151
- Tractor
- Iseki 2140
I've seen a number of bucket designs by fellow members, many seem to be of an angular design. This has got me thinking, as I've always made mine with a rounded back and flat top as shown in the image below
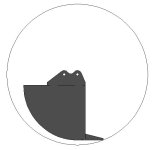
My reasoning for the flat top is that its then easy to see the bucket is flat and ready to draw back toward yourself.
My reasoning for the rounded back is mainly for the easy flow of soil into the back of the bucket, though I suppose an angular design would help break-up the soil. Another feature of my round design is to maximise the area within the 'swing' area of the bucket so it continues to dig without being pushed out by the back of the bucket.
A note of caution. many mini diggers come with buckets that are far too small, so a bigger bucket reduces digging time, but... do be careful not to oversize your bucket as if your digger has short out-riggers/steadies, its quite easy to tip your machine over by having an over-weight bucket with soil out-side the safety lift zone of your out-riggers.
What's the experience of others?
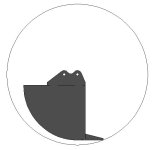
My reasoning for the flat top is that its then easy to see the bucket is flat and ready to draw back toward yourself.
My reasoning for the rounded back is mainly for the easy flow of soil into the back of the bucket, though I suppose an angular design would help break-up the soil. Another feature of my round design is to maximise the area within the 'swing' area of the bucket so it continues to dig without being pushed out by the back of the bucket.
A note of caution. many mini diggers come with buckets that are far too small, so a bigger bucket reduces digging time, but... do be careful not to oversize your bucket as if your digger has short out-riggers/steadies, its quite easy to tip your machine over by having an over-weight bucket with soil out-side the safety lift zone of your out-riggers.
What's the experience of others?