bumperm
Veteran Member
Ultra High Molecular Weight Polyethylene (or UHMW PE for short) is the strongest long chain polymer plastic available. It is also blessed with a coefficient of friction that rivals Teflon. Thus it is particularly suitable for high wear and abrasion applications where slippery is good too! Snow blowers come to mine, snow does not stick well to UHMW, so clogs, even with slushy snow, are rare. Throw distance can increase by 25%, maybe more :thumbsup:.
UHMW is a thermoplastic, so can be bent and shaped with heat, a heat gun works well, as does a propane torch if you are careful. The plastic will turn from opaque white to clear as it is heated. It must be held in place as as it is cooled. UHMW can be easily cut or machined with common woodworking tools, saws etc.
Lining the chute was the first project (and was written up in another post previously - though I think the photo links no longer work):

Last week I lined the impeller housing (hasn't been tested in the white stuff yet).
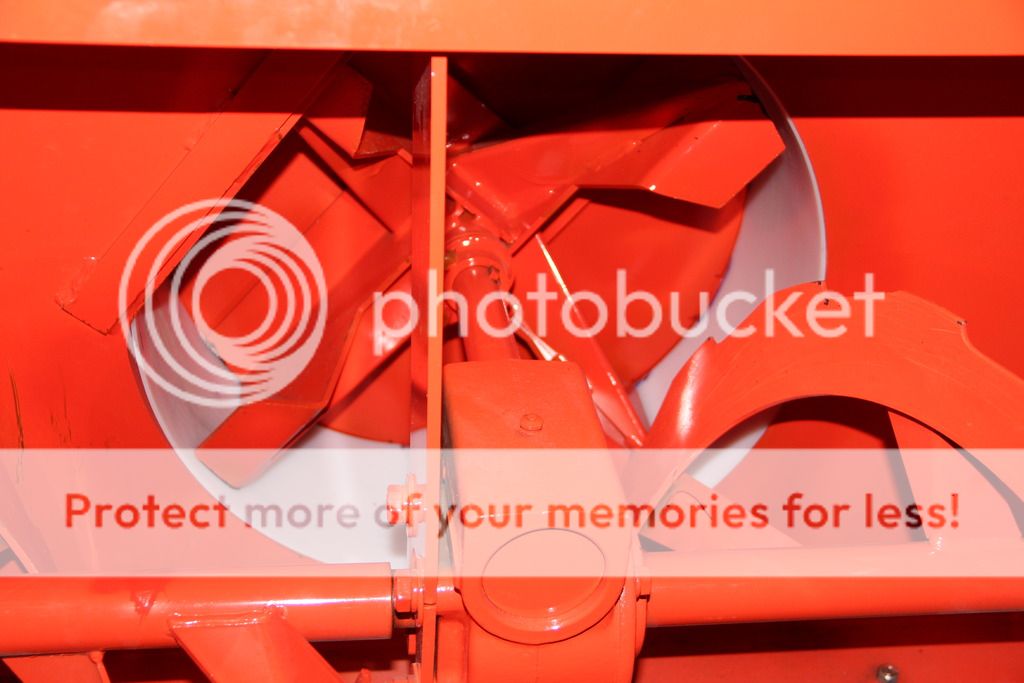
The UHMW used is 1/8" thick, 64" long by 6 - 7/8" wide. The acute angle bend (bottom in picture below or left side blower from cab), is about 35 degrees and is fully heat formed and fitted by first doing the larger bend outside the blower, then the side angles are bent and clamped in place after sliding the straight end of the UHMW into the housing in direction of impeller rotation. Then removed again. Since the liner has to be removable and insertable for fitting and replacement, (top in photo) cannot be heat formed. Instead a "V" chisel used in wood carving was used to carve a groove in the plastic on the inner surface to allow the side "ears" to be bent into position. Note the plastic isn't pulled tightly into position against the housing, but with snow pressure I'm sure it will conform - in any case not an issue.
Only the acute angle end at the "beginning" of the impeller housing is fixed in place with two 10-32 SS machine screws into drilled and threaded holes in chute (bottom of next picture). The exit end of liner (top in photo) is slotted for a single 10-32 SS screw, fender washer, and locknut - adjusted just snug. This is to allow for the thermal coefficient of expansion differential between the plastic and steel. (I put the UHMW in the freezer, measured length, then soaked it in my hot tub. The 64" length grew by 1/2", so that's how long the slot is.
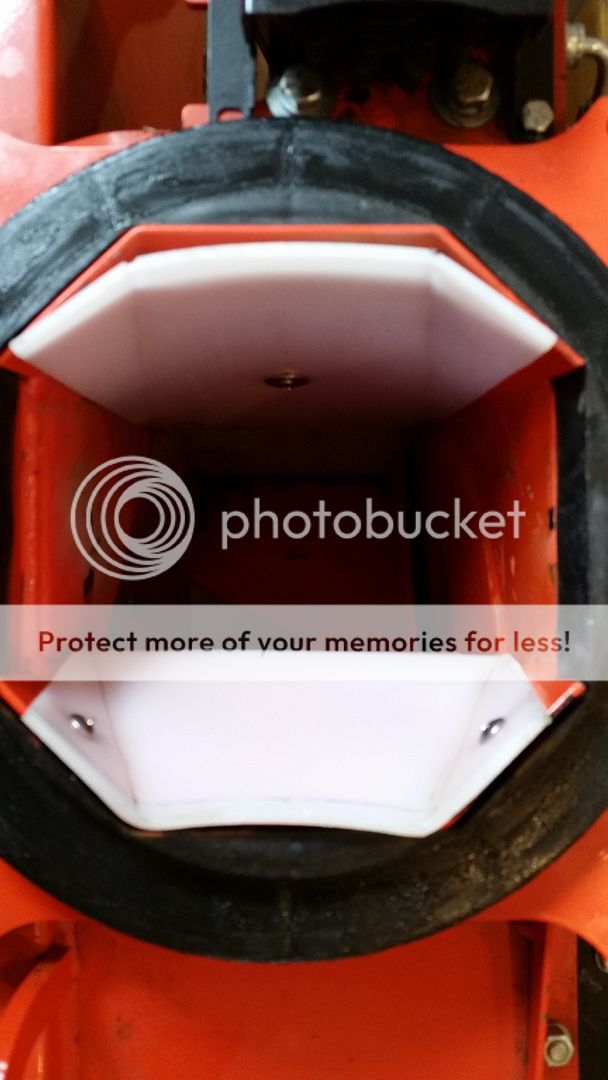
Looking down the chute:

Should mention that I removed a small amount of material from the impeller blades to provide clearance for the liner. The blades were not all exactly the same length, so I used layout dye (Dy-Kem) and a divider to scribe a line off the face of the blower housing onto each blade - then had at it with angle and die grinders to get all the blades the same and a good snug fit to the liner with little friction - (a right angle air die grinder with 3M rol-loc sanding disks provided a smooth final surface to the blade ends). Dy-Kem was also useful for the grinding process as it made it easier to see where material was being removed when the dye was repeatedly brushed on the high spots.
Now where is the snow . . .
bumper
UHMW is a thermoplastic, so can be bent and shaped with heat, a heat gun works well, as does a propane torch if you are careful. The plastic will turn from opaque white to clear as it is heated. It must be held in place as as it is cooled. UHMW can be easily cut or machined with common woodworking tools, saws etc.
Lining the chute was the first project (and was written up in another post previously - though I think the photo links no longer work):

Last week I lined the impeller housing (hasn't been tested in the white stuff yet).
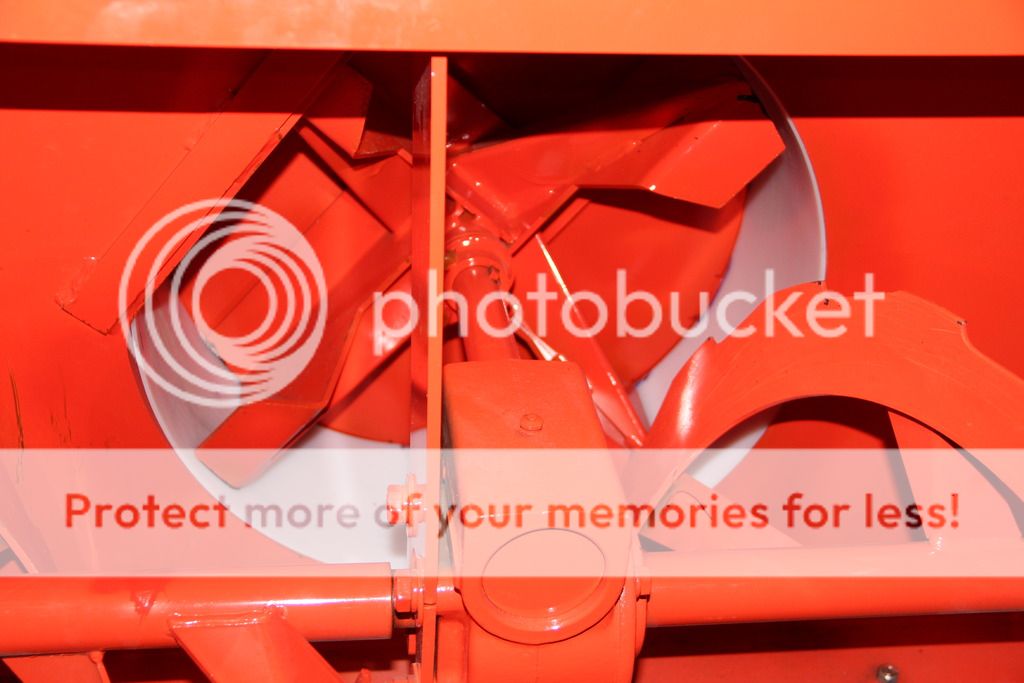
The UHMW used is 1/8" thick, 64" long by 6 - 7/8" wide. The acute angle bend (bottom in picture below or left side blower from cab), is about 35 degrees and is fully heat formed and fitted by first doing the larger bend outside the blower, then the side angles are bent and clamped in place after sliding the straight end of the UHMW into the housing in direction of impeller rotation. Then removed again. Since the liner has to be removable and insertable for fitting and replacement, (top in photo) cannot be heat formed. Instead a "V" chisel used in wood carving was used to carve a groove in the plastic on the inner surface to allow the side "ears" to be bent into position. Note the plastic isn't pulled tightly into position against the housing, but with snow pressure I'm sure it will conform - in any case not an issue.
Only the acute angle end at the "beginning" of the impeller housing is fixed in place with two 10-32 SS machine screws into drilled and threaded holes in chute (bottom of next picture). The exit end of liner (top in photo) is slotted for a single 10-32 SS screw, fender washer, and locknut - adjusted just snug. This is to allow for the thermal coefficient of expansion differential between the plastic and steel. (I put the UHMW in the freezer, measured length, then soaked it in my hot tub. The 64" length grew by 1/2", so that's how long the slot is.
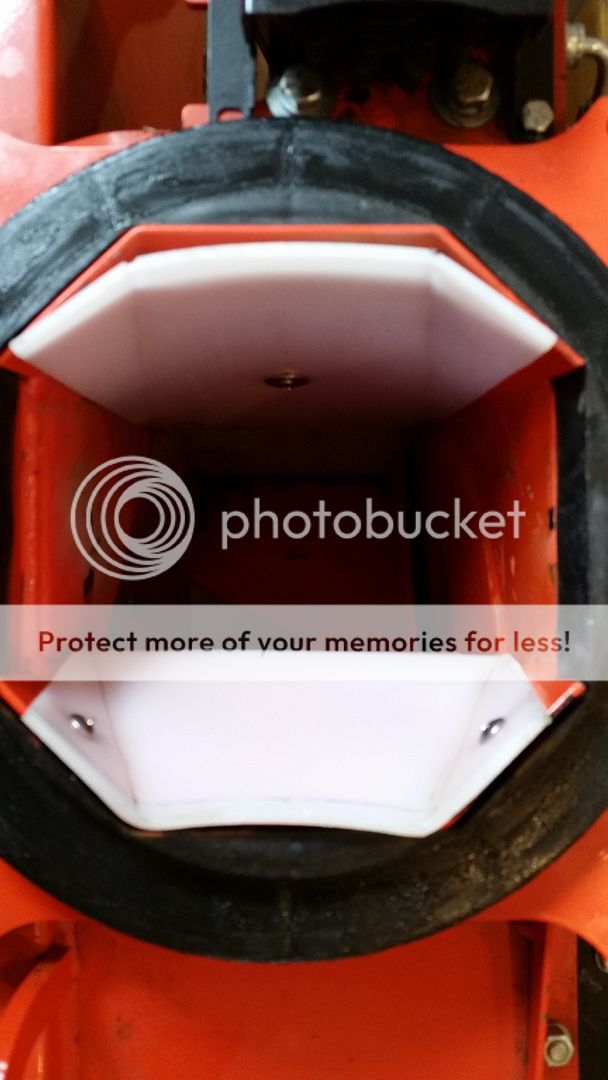
Looking down the chute:

Should mention that I removed a small amount of material from the impeller blades to provide clearance for the liner. The blades were not all exactly the same length, so I used layout dye (Dy-Kem) and a divider to scribe a line off the face of the blower housing onto each blade - then had at it with angle and die grinders to get all the blades the same and a good snug fit to the liner with little friction - (a right angle air die grinder with 3M rol-loc sanding disks provided a smooth final surface to the blade ends). Dy-Kem was also useful for the grinding process as it made it easier to see where material was being removed when the dye was repeatedly brushed on the high spots.
Now where is the snow . . .
bumper