Good news, I found the problem with my hydraulics. First of all, thank you to everyone who contributed to this post and for all the advice. I have learned quite a bit through this process and certainly picked up some great troubleshooting advice along the way. It is great having members on this forum who are willing to help out and share their knowledge.
Over the weekend, I found out that we are expecting 12-15 inches of snow (I live in SE Minnesota) so I ran my tractor into the shop to work on this on-going hydraulic issue of losing my rear hydraulics and 3 point hitch arms. Before digging in, I threw up a quick prayer to the Lord to make this a simple fix and then got started. To those just jumping in,originally I had added a rear single spool remote about two months ago so that I could have hydraulic chute rotation on my 3 pt snowblower. I had used it for several snow clearings and all went well. During the last snowfall however, while blowing snow, I lost hydraulics to the rear and my remote to move the chute quit working as well as my lift on my 3 point arms. I visually checked everything, looked for seepage, broken linkage etc and to no avail found nothing that seemed out of sorts. My front end loader worked but no rear hydraulics. I also observed the hydraulic pump got real hot in the time it took me to get from the road back to shed to park it.
I was convinced I either had a fault in the rear remote spool or that I had blown a seal in the piston cylinder that operates the three point lift. I was just getting ready to do some mechanical diagnosis and I remember that on my diverter block their is a control screw that you can turn to control the three point linkage and another way to control auxilary equipment operation such as a backhoe. See photo:
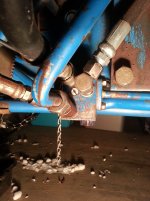
In the manual it describes turning it left for the auxilary equipment and . It has always been set to the left as long as I have owned the tractor. At one time the prior owner had plumbed in lines to run a back hoe which meant hooking up a line when you wanted the backhoe and unhooking it when wanting the loader. I had never messed with it but thought just for kicks, I will turn the control screw to the right (right for the three point linkage) and see what happens. After turning it, I fired up the tractor and low and behold, the three point arms operated. AHA... they do work. I raised them up, and then watched for them to fall thinking I may have a bad piston seal. Nothing happened - they held tight. I then played with the know that controls the rate of drop and it too seemed to work as it should. All was well but then I tried my loader and there was nothing. No pressure at all and the loader would not work. So, I turned the control screw back to the left and AHA... loader works just fine but now no rear hydraulics again. This is odd, the rear obviously works and the front obviously works but independent of each other and no longer at the same time. So now I amd focusing on the diverter block.
I started looking closer at it and then wiggled my hose from the loader spool going into the inlet port on the diverter block.
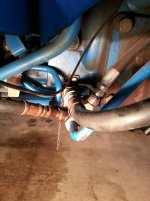
It had a little play at the coupler and seemed a little loose. I tried raising the loader again and this time, hydraulic oil started seeping out of the quick coupler on the hose going into the inlet port. Not good I thought but maybe I getting somewhere I thought. I wiped the coupler clean and wiggled the hose again and in the process I realized the hose was not fully engaged into the coupler. I pulled lightly on it and it came right out. So by this time I am thinking...."could I really be this blessed??? Is this it?" I checked the coupler and found the O-ring to be intact. I quickly cleaned it up and reconnected the hose into the coupler. Gave it a light tug and it held just fine - the coupler is holding as it should. I set the control screw on the diverter block back to the original setting and fired up the tractor and AHA.... everything works again just as it should. The loader worked fine, plenty of pressure to lift the front off the ground with the bucket, and three point had plenty of lift for the blower and it held it up with no settling, and the rear remote operated the chute and as it should. Also, the hydraulic pump did NOT heat up at all. YEEHAW!
What is odd is how the coupler came lose enough to release but did not leak until I wiggled it. I park in the shed with a cement floor so I would have noticed any puddles. Last fall I was clearing some brush in our woods and I guess it is possible a stick or something could have bump the coupler enough to partially release it. The hose going into the intlet port is very stiff so in theory, it could have stayed in put until it got to a point where it finally popped out. Stranger things have happened. All I know is that it is working well now and I did go back out Sunday afternoon and blew snow again for a half hour and all worked just fine. I have attached four photos in this post for those who are interested. The first shows the diverter block with the control screw. The second shows the diverter block with a better view of the inlet hose (black hose on upper left) coming from the loader spool. The last two show the instruction from the owners manual describing the control screw settings on the diverter block.
Thanks again to all! I will provide one final round of updates to let you know how it goes after getting through the winter storm that is upon us today.