KennyG
Elite Member
I really admire the fabrication tables some of you have but I can't really justify all that for the welding I do. I did, however, recently make a small welding table out of a salvaged Craftsman table saw. I bought the worn out table because I have the same model and needed the fence and work guide. I stripped the guts out of it and added casters from a $8 Harbor Freight furniture dolly. When I find the right material I will replace the wood shelves with metal. It's pretty handy for welding small stuff and as a general work table.
In addition to the parts I needed, the old saw had a new fine tooth blade and the motor seems to run OK, although I'm not sure what the keyway will look like when I finally get the pulley off.
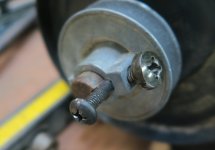
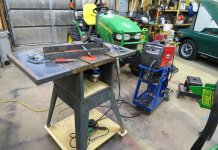
In addition to the parts I needed, the old saw had a new fine tooth blade and the motor seems to run OK, although I'm not sure what the keyway will look like when I finally get the pulley off.
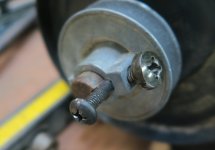
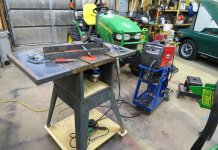