Okay, after a month of re-design, cutting, and welding including a two-week diversion which I'll explain later, the harrows are finished.. again! The pics with yellow lines show where I cut the frames, axles and other parts (including myself!), the ones with green arrows show which parts were added.
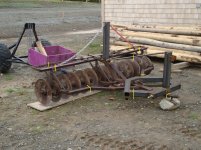
I shortened the tongue again by about 18-20 inches, cut 7 inches off both axles, and narrowed the frame that hangs the bearing housings in the initial phase of the project. That also required cutting and redesigning the angle adjusters for the front gangs.
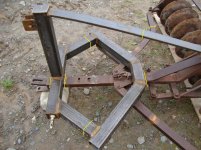
It just about choked me to cut that 3 inch square tube, after all the time I spent getting the angles just right a year and a half ago.
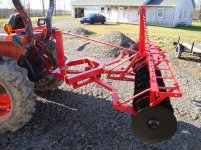
The frames that sandwiched the angle adjusters were lost as part of the process, which gave me some concerns about the stiffness of the whole thing. All that would have held it from twisting were the welds holding the tongue to the 3-point frame. I don't do too bad a job at welding by amateur standards, but everything has it's limits. More on that in the next post.
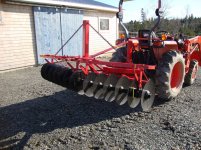
The bearing assemblies are pretty simple, just a piece of hex stock with an inner rotating sleeve that gets grease from the back. The hex stock is held in place by a semi-hexagonal shape in the bearing holder halves which are then bolted together. The only grease seals are short lengths of rope held by grooves in the bearing holders. I doubt they're very effective at keeping grease in, but that was the fashion when these were built.
Sean