polemidis
Gold Member
Hello, I am building a Firewood processor and the frame and mechanical staff are close to be done. I need a little help with the hydraulic circuit. In order to keep things simple for now, and to work with what I have in hand as much as possible, I removed the splitter circuit. It will run separate with its own gas engine and 2-stage pump.
So here is where I am with my homework firewood proceesr vbom - Google Slides
Its a google slide, feel free to duplicate the page and make edits if its easier for you.
Can you see any mistakes? Do I need something else? Is there anyway to improve the circuit or is there anything that will cause me trouble?
I studied the manifold of the 9kproducts with all the cartdridges, and I think its too advanced for me, and I do not even know how to make it, so I ended up with the above design.
Any insights plz?
I know there are some hydraulic gurus in here! And I do not have a hydr. shop closeby to me
P.S. I did study all the other related posts in TBNforums, which helped me to end up with that circuit.
I am also attaching the image if its more convenient for you guys.
EDIT: Also I was wondering where and how many pressure gauges should I install in order to troubleshout/tune the circuit.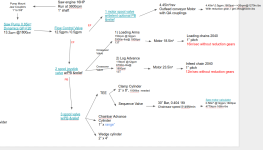
So here is where I am with my homework firewood proceesr vbom - Google Slides
Its a google slide, feel free to duplicate the page and make edits if its easier for you.
Can you see any mistakes? Do I need something else? Is there anyway to improve the circuit or is there anything that will cause me trouble?
I studied the manifold of the 9kproducts with all the cartdridges, and I think its too advanced for me, and I do not even know how to make it, so I ended up with the above design.
Any insights plz?
I know there are some hydraulic gurus in here! And I do not have a hydr. shop closeby to me
P.S. I did study all the other related posts in TBNforums, which helped me to end up with that circuit.
I am also attaching the image if its more convenient for you guys.
EDIT: Also I was wondering where and how many pressure gauges should I install in order to troubleshout/tune the circuit.
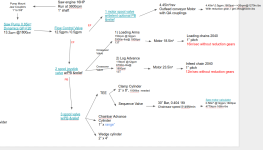
Last edited: