OK, Time to revive this. I haven't had a lot of time to practice welding the past couple months, but today I had a free day and nothing to do, and it occurred to me I needed to get back to this. So I looked over this thread and tried a few things. Executive summary: There must be some catch to this that I am not getting.
I grabbed a couple scrap cutoffs of 3/8" angle to use as practice. I figured I would weld in the corner like a fillet. I tried all manner of the suggestions on this thread. There was only one time I said to myself that it didn't look like total ****. The root problem is the same as earlier - the weld pool metal drips. Here is a small 3/8" fillet coupon I did for some comparison after some other practice. I did 3 different welds on this to compare - flat position, Vertical down, and vertical up. Pictures don't seem to be as good as looking at it live, but the flat and V Down looked pretty similar. The V up was one of the best ones I did, and I would still say it looks like crap.
You can see the conditions on the coupon - about 420 ipm, 150A or so (I don't think to look at the display much), and 23v with 035 wire. These figures are right off the Miller "calculator" I have.
Here is a better example of the crap I was still getting:
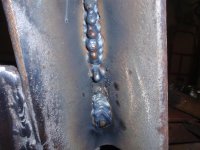
Note the section of Vert up at the top (drip, drip, drip) and the Vert down at the bottom (smooth but not well tied-in, in this case, especially on the left)
I tried a few things here in Vert up. Gun angle - I kept it perpendicular (0 deg) and about 15-20 pointed up. I had slightly better success with 0, but not much. I did some major work on wire feed at the same voltage. The charts recommend 23-24v, 420-520 ipm for 035 wire on 75/25 gas. I tried that, and then dialed the wire down to 250-300 ipm also. I got better looking welds at the low speeds, but it did not sound like normal MIG welding. I'd be concerned it was cold, but I can't be sure.
I'm sure my technique is the fault, but I have no idea what to change after all this. I have tried everything that has been suggested and everything I can think of from what I know. Nothing looks good enough to pass in my vertical ups at this point. Open for suggestions, but not sure how much help I can get without it being in-person at this stage...