3RRL
Super Member
- Joined
- Oct 20, 2005
- Messages
- 6,825
- Tractor
- 55HP 4WD KAMA 554 and 4 x 4 Jinma 284
I don't think this would be difficult at all to fabricate and could be close to trivial for a shop with a CAD system plasma cutter and any 220v welder. I'd think about 1/2 mild steel (??maybe more)would provide sufficient material strength for an 18 inch ripper for my Woods BH90x but that is just guess.
Island,
You know that articulating mechanical thumb I made for may backhoe?
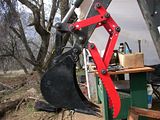
Well, I used 2 pcs of 1/2" thick material in several places. They ended up bending easily and I had to replace them with 1" thick...2 places mind you. I would consider 1-1/2" thickness for the ripper shank as a minimum. You could do that by welding 2 scarifiers together.
Another thing I would do is make (or buy) the tooth so it is at least 2" wide and then weld a blade on top of the shanks so I could sharpen it. Why?
The tooth is for digging and the sharpened top of the shank blade would be for cutting and ripping the roots. It should not be thin like a knife blade but more blunt and wide like a wedge. You are right about having minimal ground disturbance that way. I have thought about making one myself, but it's way down my list of priorities at this time.
Island,
You know that articulating mechanical thumb I made for may backhoe?
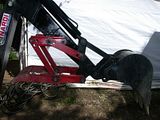
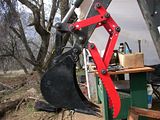
Well, I used 2 pcs of 1/2" thick material in several places. They ended up bending easily and I had to replace them with 1" thick...2 places mind you. I would consider 1-1/2" thickness for the ripper shank as a minimum. You could do that by welding 2 scarifiers together.
Another thing I would do is make (or buy) the tooth so it is at least 2" wide and then weld a blade on top of the shanks so I could sharpen it. Why?
The tooth is for digging and the sharpened top of the shank blade would be for cutting and ripping the roots. It should not be thin like a knife blade but more blunt and wide like a wedge. You are right about having minimal ground disturbance that way. I have thought about making one myself, but it's way down my list of priorities at this time.