s219
Super Member
- Joined
- Dec 7, 2011
- Messages
- 8,548
- Location
- Virginia USA
- Tractor
- Kubota L3200, Deere X380, Kubota RTV-X
This addition was long overdue -- I have owned my L3200 for 3 years now, and have been wanting a ballast box the whole time. I had been using my box blade for ballast, but it was large and unwieldy, and there were a lot of cases where I skipped using any ballast because the box was too much trouble or too big for what I was doing. Besides, the 5' box blade is only about 450# and I knew heavier ballast was needed.
After looking around, I settled on the Kubota B8160 ballast box for $240. This is actually sized for B and BX models, but I liked the size and the fact that it was about half the price of the larger L8170 ballast box intended for L models. Other than size, the two boxes are constructed about the same.
For my uses, the box would need to have some sort of trailer hitch capability, and be able to move my fully loaded 7x16 trailer and deal with 700-1000# of tongue weight. I decided to weld up a heavy-duty trailer hitch frame that could drop inside the box, which was a fun fabrication project. I did some fitting and welding inside the box, and some outside the box, with the end product able to slip out of the box for painting and back into the box for final installation. Here are a few pics of that build process:
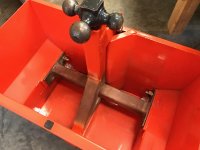
I designed and sized the hitch frame to be standalone in capability and not depend on the box itself for structure. I am sure it's overkill, but I just didn't want to depend on the box itself (and any filler) to handle a heavy tongue weight load. The top of the hitch frame post was left open to provide a storage spot for my drawbar (it also will fit a shovel handle just fine, which came in handy today).
Once the frame was done, it was time to fill the box. I decided on a combination of concrete and scrap metal -- the latter to help boost the weight back up into "L series" territory while using a smaller-volume "B/BX series" box. I had some scrap rebar that had fallen off a truck on my road and was too mangled to use, so I cut that into 1' and 2' pieces. I was also able to get a bucket of used lead wheel weights from a tire shop. I first poured concrete in the bottom 1/3 of the box to encapsulate the lower hitch frame. After that cured, I then layered in concrete, rebar, and lead.
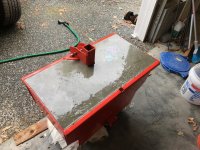
All said and done, the box weighs around 820# based on the actual weight of materials I put in, the weight of the hitch frame, and the 100# weight of the box itself. Here are a couple installed pictures:
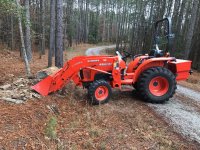
The distance from the front loader bucket center to the front axle is approximately 4' and the distance from the front axle to the ballast box center is approximately 8.5'. Running the math, that tells us that the 820# rear ballast will counteract 1742.5# of weight in the front bucket, which will cover my needs very well.
The box makes the tractor feel completely different and a lot more settled in general. I can only assume my front axle had been suffering before this! When lifting some heavy logs on a down slope, where I had formerly always needed 4WD to back up, the ballast allows the tractor to reverse in 2WD with no slip at all. That is a pretty cool demonstration of the benefit.
After looking around, I settled on the Kubota B8160 ballast box for $240. This is actually sized for B and BX models, but I liked the size and the fact that it was about half the price of the larger L8170 ballast box intended for L models. Other than size, the two boxes are constructed about the same.
For my uses, the box would need to have some sort of trailer hitch capability, and be able to move my fully loaded 7x16 trailer and deal with 700-1000# of tongue weight. I decided to weld up a heavy-duty trailer hitch frame that could drop inside the box, which was a fun fabrication project. I did some fitting and welding inside the box, and some outside the box, with the end product able to slip out of the box for painting and back into the box for final installation. Here are a few pics of that build process:
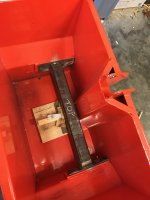
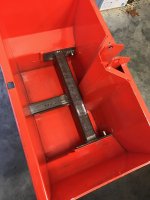
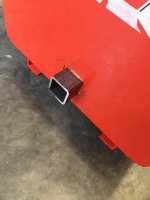
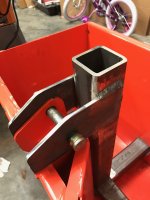
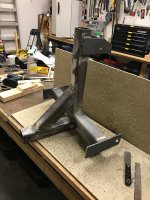
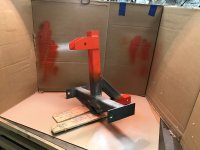
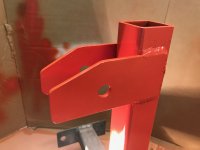
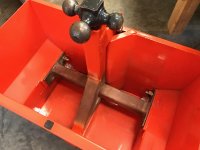
I designed and sized the hitch frame to be standalone in capability and not depend on the box itself for structure. I am sure it's overkill, but I just didn't want to depend on the box itself (and any filler) to handle a heavy tongue weight load. The top of the hitch frame post was left open to provide a storage spot for my drawbar (it also will fit a shovel handle just fine, which came in handy today).
Once the frame was done, it was time to fill the box. I decided on a combination of concrete and scrap metal -- the latter to help boost the weight back up into "L series" territory while using a smaller-volume "B/BX series" box. I had some scrap rebar that had fallen off a truck on my road and was too mangled to use, so I cut that into 1' and 2' pieces. I was also able to get a bucket of used lead wheel weights from a tire shop. I first poured concrete in the bottom 1/3 of the box to encapsulate the lower hitch frame. After that cured, I then layered in concrete, rebar, and lead.
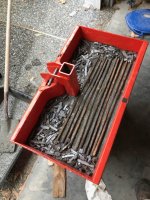
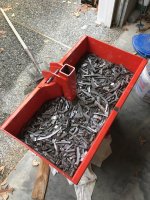
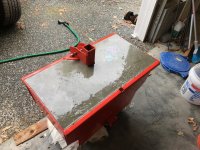
All said and done, the box weighs around 820# based on the actual weight of materials I put in, the weight of the hitch frame, and the 100# weight of the box itself. Here are a couple installed pictures:
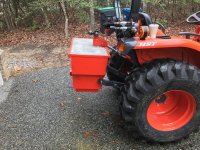
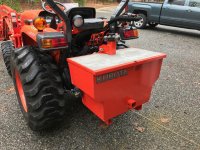
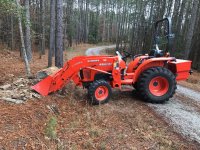
The distance from the front loader bucket center to the front axle is approximately 4' and the distance from the front axle to the ballast box center is approximately 8.5'. Running the math, that tells us that the 820# rear ballast will counteract 1742.5# of weight in the front bucket, which will cover my needs very well.
The box makes the tractor feel completely different and a lot more settled in general. I can only assume my front axle had been suffering before this! When lifting some heavy logs on a down slope, where I had formerly always needed 4WD to back up, the ballast allows the tractor to reverse in 2WD with no slip at all. That is a pretty cool demonstration of the benefit.
Attachments
Last edited: