sd455dan
Elite Member
- Joined
- Oct 23, 2012
- Messages
- 4,781
- Location
- North Idaho
- Tractor
- Rhino 554, Ford 550 TLB (JD X500, MTD, Gilson riding mowers) Ford 3000-Sold
Got a Buick V6 in trade to help my son (shoe horn) a 350 Olds in to a 3rd gen Camaro.
The V6 had the left top engine to transmission ear snapped off at some point in the past.
Wanted to give repairing (building up) a new mount a try.
I have only tried repairing 1 other cast project - mig welding a cracked intake back together.
bought a couple sticks of 1/8 rod for cast iron at the local Co-Op- and all he knew was the sticks were for cast, they were marked NA 111
The only reference I could find to these rods was an old post by Shieldarc and Yomax. Thinking these were on the shelf for a long time. but sounded like they were a good repair rod that was also machinable.
Anyway ground out the sides and since there was about 1/2 of the threads left on the bottom it occurred to me that if I could find a piece of tube or round stock of aluminum or another metal that the cast rod would not stick to it might save some time and work trying to bore and re-thread the hole.
I did find a piece of tubing and clamped it in place hooked up my little 3 in 1 inverter found a chart that said to run cast rod DC+ tried 1 short weld on an old junk head to get the amps close and did a little local pre heat.
Ran single 1/2 inch beads and worked my way around the tube after letting each weld cool while peening the beads.
Did get some inclusions but can't find any actual cracks
it is not pretty but after a bit of grinding and light drilling was able to run a tap through it.
Again Not pretty for sure- but I think it will work.
And it was fun trying a new new stick welding process.

The V6 had the left top engine to transmission ear snapped off at some point in the past.
Wanted to give repairing (building up) a new mount a try.
I have only tried repairing 1 other cast project - mig welding a cracked intake back together.
bought a couple sticks of 1/8 rod for cast iron at the local Co-Op- and all he knew was the sticks were for cast, they were marked NA 111
The only reference I could find to these rods was an old post by Shieldarc and Yomax. Thinking these were on the shelf for a long time. but sounded like they were a good repair rod that was also machinable.
Anyway ground out the sides and since there was about 1/2 of the threads left on the bottom it occurred to me that if I could find a piece of tube or round stock of aluminum or another metal that the cast rod would not stick to it might save some time and work trying to bore and re-thread the hole.
I did find a piece of tubing and clamped it in place hooked up my little 3 in 1 inverter found a chart that said to run cast rod DC+ tried 1 short weld on an old junk head to get the amps close and did a little local pre heat.
Ran single 1/2 inch beads and worked my way around the tube after letting each weld cool while peening the beads.
Did get some inclusions but can't find any actual cracks
it is not pretty but after a bit of grinding and light drilling was able to run a tap through it.
Again Not pretty for sure- but I think it will work.
And it was fun trying a new new stick welding process.
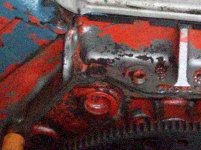




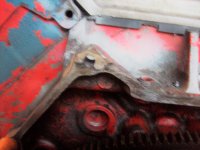
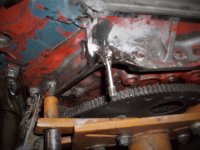

Last edited by a moderator: