jimcolt
Gold Member
An often discussed subject regarding thermal cutting of metal is with edge angularity. When cutting with a plasma or oxy-fuel hand torch this is usually a moot point, as the human brain ( a very nice cnc control system!) can compensate with infinite variations in the holding angle of the torch. With mechanized and cnc cutting machines that generally need to hold the torch perpendicular to the material being cut there still is a level of angularity that will vary from system to system based on design, will vary based on the particular setup (cut height, cut speed, power level, etc.) and certainly will vary based on the condition of the consumable parts that actually generate the high temperature, high velocity cutting jet.
I have spent a fair amount of my last three decades helping plasma system users achieve the best possible performance from their plasma systems.....and this topic is among the busiest! Plasma cutting torches all swirl the cutting gas (usually air in low cost plasma systems), the swirling was primarily developed to minimize edge bevel, and while the actual physics of how the swirling gas does this is fairly complex, the swirl actually shifts the bevel towards the left or right depending on the direction that the swirl is forced (counter clockwise or clockwise). With a clockwise swirl (99% of plasma torch designs use only CW swirl) expect the least edge angularity will always be on the right side of the torch as the torch is moving away from you cutting into a plate. So.....when you need to cut a part like a ring with an ID and an OD, the inside of the ring should be cut on the CCW direction, the outside contour in the CW direction.....this keeps the expected good side of the cut on the "keeper" edges of the part, worse angularity on scrap parts. There are special consumables available for some models of high definition (read: expensive industrial) plasma's that reverse the swirl...often used when two or more torches are cutting mirror image parts simultaneously....but this generally does not apply to air plasma systems.
Another thing that causes angularity is the actual heat and friction of melting metal, then blowing it out of the bottom of the plate using a high velocity, 25,000F jet. As material gets thicker the top of the cut absorbs much of the energy, and the friction of the molten metal trying to eject out the bottom of the cut makes the width of the cut wider at the top, narrower at the bottom. By using the swirl techniques listed above.....this whole cut kerf is shifted a bit...leaving the edge with better squareness to the right.
Keep in mind that regardless of brand or model, you will not get zero bevel with even a high definition industrial plasma. For that matter you will not get zero bevel with a laser or abrasive waterjet cutter as well. There are some high end laser water jet and high def plasma cutters that can get close, and some even have complex bevel mechanisms on the torch carriage to compensate for bevel. I have certainly heard many claims of "zero bevel", however upon close inspection and measurement with a precision angle measuring tool or a CMM (coordinate measurement machine) you will always find some measure of angularity as well as variation in angularity.
Two basic types of bevel that you should look for....is with bevel angle that varies wildly around the perimeter of a part, and bevel angle that may be severe, but is consistent around the perimeter.
Varying bevel is usually caused by 1. Damaged consumables, usually the nozzle. If the nozzle is incorrectly position (proper pierce height) when piercing thick materials....expect the orifice to become damaged (nicks, notches, out of roundness, etc), and since the nozzle shapes the arc.....expect the arc to exit the torch with an out of round shape and with inconsistent angularity. 2. Blocked airflow, incorrect air pressure settings, incorrectly manufactured consumables can also cause varying angularity. 3. Torch is not perpendicular to material.
Consistent bevel is a sign that all of the above is probably ok, but you need to fine tune the process, which is commonly done this way. 1. review the torch height settings, ensure the torch is always maintaining the correct cut height (which is always lower than the pierce height) and that the height control system on the cnc machine is function as it should. Too high equals more bevel, period. 2. Make sure (for least bevel) that you are using the lowest amperage consumable set for the material you are cutting...and that you are operating these consumables at the max rated amperage and air flow settings. Too much power gives you speed, but hurts angularity.
Height affects bevel , cut speed affects bevel. Design of the plasma torch affects bevel. Wear on consumables affects bevel. Incorrect gas flows, impurities in the plasma gas (air) will also affect bevel.
To get the best (least) bevel with an air plasma, choose the set of lowest amperage consumables for your torch that the manufacturer suggests will cut the material, then follow the cut charts specs.....especially cut height and optimum speed. Lower speed will sometimes improve angularity, but also increases dross.
Since I use Hypertherm plasma cutters, I will use them as an example. With my Powermax85 (Hypertherm) I have a choice of fine cut consumables (rated for 10 gauge and thinner), 45amp shielded (gauge through 3/8"), 65 amp shielded (10 gauge through 5/8") and 85 amp shielded (3/16" through 1-1/4"). If I want to cut 1/4" steel.....I can choose any set of consumables except the Finecuts. If I use 85 amps, I will cut very fast, the cut edge will have zero dross, the edge will have top edge rounding and fairly severe bevel. If I choose the 45 amp set.....the 1/4" will have approximately 2 to 2.5 degrees bevel, clean sharp top and bottom edges and slower cut speeds.
Many try to use the high powered consumables....and simply reduce the amperage and the speed. In simple terms....larger cutting nozzles have a larger orifice to shape the arc. By turning down the amperage on a large nozzle....you are dramatically reducing arc energy density....which softens the arc. This low energy density arc often creates a concave or convex cut edge, virtually eliminates the dross free speed range.....producing a drossy, ugly cut. Using a smaller nozzle at its max rated amperage gives you lower power with high energy density, The energy density of a Hypertherm 45 amp nozzle running at 45 amps is the same as an 85 amp nozzle running at 85 amps, roughly 12,000 amps per square inch.
Bottom line....if you want the best cut quality throughout a wide thickness range....a plasma system that offers a wide choice of consumable parts (for fine tuning quality and speed) is necessary. If the cut quality is not of biggest concern, then you may not need this type of feature in a system.
Attached are a couple of pics of 3/8" steel cut at 45 amps with a 45 amp nozzle. The edge angularity numbers are written on the top for each side......degrees from 90. I consider the small variation in angularity on this part as "consistent angularity. Most users would look at this part (without measuring angularity) and call the edges square...as they do appear quite nice.
The third pic is from an LS1 motor mount I made from 1/4" steel, as cut. If you look closely you will see "tab and slot" design which allows you to plug weld the sides to the base eliminating fixturing and making for a better looking assembly. Low cost cnc plasma machines have opened up a whole new world for us hobbyist fabricators! No grinding, no rework!
Jim Colt


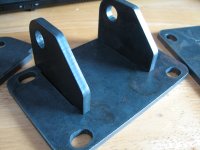
I have spent a fair amount of my last three decades helping plasma system users achieve the best possible performance from their plasma systems.....and this topic is among the busiest! Plasma cutting torches all swirl the cutting gas (usually air in low cost plasma systems), the swirling was primarily developed to minimize edge bevel, and while the actual physics of how the swirling gas does this is fairly complex, the swirl actually shifts the bevel towards the left or right depending on the direction that the swirl is forced (counter clockwise or clockwise). With a clockwise swirl (99% of plasma torch designs use only CW swirl) expect the least edge angularity will always be on the right side of the torch as the torch is moving away from you cutting into a plate. So.....when you need to cut a part like a ring with an ID and an OD, the inside of the ring should be cut on the CCW direction, the outside contour in the CW direction.....this keeps the expected good side of the cut on the "keeper" edges of the part, worse angularity on scrap parts. There are special consumables available for some models of high definition (read: expensive industrial) plasma's that reverse the swirl...often used when two or more torches are cutting mirror image parts simultaneously....but this generally does not apply to air plasma systems.
Another thing that causes angularity is the actual heat and friction of melting metal, then blowing it out of the bottom of the plate using a high velocity, 25,000F jet. As material gets thicker the top of the cut absorbs much of the energy, and the friction of the molten metal trying to eject out the bottom of the cut makes the width of the cut wider at the top, narrower at the bottom. By using the swirl techniques listed above.....this whole cut kerf is shifted a bit...leaving the edge with better squareness to the right.
Keep in mind that regardless of brand or model, you will not get zero bevel with even a high definition industrial plasma. For that matter you will not get zero bevel with a laser or abrasive waterjet cutter as well. There are some high end laser water jet and high def plasma cutters that can get close, and some even have complex bevel mechanisms on the torch carriage to compensate for bevel. I have certainly heard many claims of "zero bevel", however upon close inspection and measurement with a precision angle measuring tool or a CMM (coordinate measurement machine) you will always find some measure of angularity as well as variation in angularity.
Two basic types of bevel that you should look for....is with bevel angle that varies wildly around the perimeter of a part, and bevel angle that may be severe, but is consistent around the perimeter.
Varying bevel is usually caused by 1. Damaged consumables, usually the nozzle. If the nozzle is incorrectly position (proper pierce height) when piercing thick materials....expect the orifice to become damaged (nicks, notches, out of roundness, etc), and since the nozzle shapes the arc.....expect the arc to exit the torch with an out of round shape and with inconsistent angularity. 2. Blocked airflow, incorrect air pressure settings, incorrectly manufactured consumables can also cause varying angularity. 3. Torch is not perpendicular to material.
Consistent bevel is a sign that all of the above is probably ok, but you need to fine tune the process, which is commonly done this way. 1. review the torch height settings, ensure the torch is always maintaining the correct cut height (which is always lower than the pierce height) and that the height control system on the cnc machine is function as it should. Too high equals more bevel, period. 2. Make sure (for least bevel) that you are using the lowest amperage consumable set for the material you are cutting...and that you are operating these consumables at the max rated amperage and air flow settings. Too much power gives you speed, but hurts angularity.
Height affects bevel , cut speed affects bevel. Design of the plasma torch affects bevel. Wear on consumables affects bevel. Incorrect gas flows, impurities in the plasma gas (air) will also affect bevel.
To get the best (least) bevel with an air plasma, choose the set of lowest amperage consumables for your torch that the manufacturer suggests will cut the material, then follow the cut charts specs.....especially cut height and optimum speed. Lower speed will sometimes improve angularity, but also increases dross.
Since I use Hypertherm plasma cutters, I will use them as an example. With my Powermax85 (Hypertherm) I have a choice of fine cut consumables (rated for 10 gauge and thinner), 45amp shielded (gauge through 3/8"), 65 amp shielded (10 gauge through 5/8") and 85 amp shielded (3/16" through 1-1/4"). If I want to cut 1/4" steel.....I can choose any set of consumables except the Finecuts. If I use 85 amps, I will cut very fast, the cut edge will have zero dross, the edge will have top edge rounding and fairly severe bevel. If I choose the 45 amp set.....the 1/4" will have approximately 2 to 2.5 degrees bevel, clean sharp top and bottom edges and slower cut speeds.
Many try to use the high powered consumables....and simply reduce the amperage and the speed. In simple terms....larger cutting nozzles have a larger orifice to shape the arc. By turning down the amperage on a large nozzle....you are dramatically reducing arc energy density....which softens the arc. This low energy density arc often creates a concave or convex cut edge, virtually eliminates the dross free speed range.....producing a drossy, ugly cut. Using a smaller nozzle at its max rated amperage gives you lower power with high energy density, The energy density of a Hypertherm 45 amp nozzle running at 45 amps is the same as an 85 amp nozzle running at 85 amps, roughly 12,000 amps per square inch.
Bottom line....if you want the best cut quality throughout a wide thickness range....a plasma system that offers a wide choice of consumable parts (for fine tuning quality and speed) is necessary. If the cut quality is not of biggest concern, then you may not need this type of feature in a system.
Attached are a couple of pics of 3/8" steel cut at 45 amps with a 45 amp nozzle. The edge angularity numbers are written on the top for each side......degrees from 90. I consider the small variation in angularity on this part as "consistent angularity. Most users would look at this part (without measuring angularity) and call the edges square...as they do appear quite nice.
The third pic is from an LS1 motor mount I made from 1/4" steel, as cut. If you look closely you will see "tab and slot" design which allows you to plug weld the sides to the base eliminating fixturing and making for a better looking assembly. Low cost cnc plasma machines have opened up a whole new world for us hobbyist fabricators! No grinding, no rework!
Jim Colt


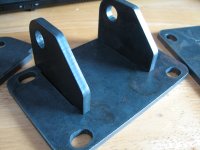
Last edited: