s219
Super Member
- Joined
- Dec 7, 2011
- Messages
- 8,548
- Location
- Virginia USA
- Tractor
- Kubota L3200, Deere X380, Kubota RTV-X
This writeup is a bit late, so I figured I'd better crank it out. We moved into a new house out in the country in May 2013, and I began working on a generator setup shortly thereafter. Based on our needs, I was looking at generators in the range of 15-20kW, and fuel choices were diesel or propane.
Propane was quickly ruled out after I was quoted a cost of $3900 from the local propane supplier to install and fill a 500 gal tank. Because we don't use propane for anything else at this new home, we would have had to purchase the tank outright and assume maintenance responsibility. Combined with the large volume of the tank, the uncertainty of propane costs over the long term, and the sometimes uncertain availability of propane delivery after major storms in this area, it then became a no brainer to go diesel.
My first choice was a 21kW water-cooled diesel unit from Central Maine diesel. It is powered by an Isuzu 4LE1 engine with a Mecc Alte alternator. The unit was assembled and shipped from Mack Boring in New Jersey. It arrived in mid-August, and I moved it into my garage while the rest of the project unfolded:

Next steps were to begin building a generator shed, run conduit from the shed site to our home, and wire things up. Here's a shot of the floor frame of my 4x8' generator shed, built from 2x6 and 2x8 lumber, as well as the conduit running in a trench to the shed:

I had approximately 100 feet of distance from the generator shed to our main panel, where our electrician had wired us with an interlock and 100A breaker to backfeed into the panel. To keep the voltage drop down over this long run, I used 1/0 aluminum wire. Here's the junction where the 1/0 comes into the home and connects up to the 2-2-2-4 feeder wire that goes into the 100A interlock breaker in the main panel:

At the other end in the shed, the wiring would go into another breaker panel near the generator, and then transition to finely stranded copper wire (4 gauge) to connect to the generator itself. The finely stranded copper wire is required for its flexibility and vibration resistance, as aluminum would eventually fatigue and fracture if connected to a generator. Here's a shot of the 4-wire copper "mining" cable I used, connecting up to the generator head:

Connectors were "cold-weld" crimped onto this mining cable with a special hexagon crimp tool, which results in near-lossless connections. Similar crimps were used to transition the finely-stranded mining cable to coarse-stranded copper for the final run into the breaker panel in the shed (required because you cannot torque down finely-stranded copper in lugs):
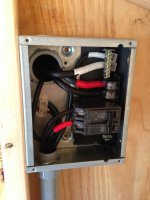
I planned to build the generator shed myself, but got tied up on a pier project that had a permit deadline. So I completed the floor and got the generator out there:

Then we hired one of the carpenters who worked on our home to build the shed to my specs, using similar materials and finishes from our home (main exception being we used T-111 siding on the shed instead of hardi-panel to keep costs down). He knocked out the shed in 4 days in did a great job:
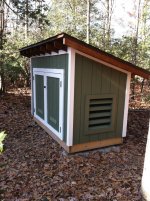
The shed has extensive venting between rafter tails to let warm air out, small intake vents down low, and two large louver vents -- one aligned with the radiator and its "pusher" fan, and the other in the opposite corner of the shed to provide makeup air. The shed also has a small door on the back to allow access to the battery, alternator, and starter.
The generator has a vertical muffler, and I got a custom tailpipe mandrel-bent so that I could route the exhaust up through a chimney in the roof:

For fuel, I am using a poly 55 gal drum (74 hours of runtime at 1/2 load). A duplex bushing (normally used for home heating oil tanks) attached to the bung on top and let me route a copper line down into the tank for a supply pickup and connect a return line:

I have a second 55 gal poly drum for reserve as needed. To bring fuel to the generator, I have a pallet-mounted 55 gal aluminum transfer tank with GPI hand pump that puts out a nice 0.5 gal per stroke, so refueling goes quickly. Here's a shot of me fueling up the tank the other night before we got hit with a snowstorm:

Finally, here are a couple movies of the generator running, with and without shed doors open:
https://vimeo.com/84737828
https://vimeo.com/84737847
Noise levels aren't too bad, but I plan to add some insulation to the shed to quiet things down a little more.
There are a lot of details I am not mentioning for brevity, so please feel free to ask questions! I should note that a local generator company quoted $10K for labor and materials to install a water-cooled generator (propane or diesel), which I initially scoffed at. But looking back and considering all the work I had to to for electrical, fuel, exhaust, mounting, etc, that $10K seems about right if I was paying someone typical trade labor rates. I saved a lot of money doing it myself, but it was a big project for sure.
thanks for reading,
219
Propane was quickly ruled out after I was quoted a cost of $3900 from the local propane supplier to install and fill a 500 gal tank. Because we don't use propane for anything else at this new home, we would have had to purchase the tank outright and assume maintenance responsibility. Combined with the large volume of the tank, the uncertainty of propane costs over the long term, and the sometimes uncertain availability of propane delivery after major storms in this area, it then became a no brainer to go diesel.
My first choice was a 21kW water-cooled diesel unit from Central Maine diesel. It is powered by an Isuzu 4LE1 engine with a Mecc Alte alternator. The unit was assembled and shipped from Mack Boring in New Jersey. It arrived in mid-August, and I moved it into my garage while the rest of the project unfolded:

Next steps were to begin building a generator shed, run conduit from the shed site to our home, and wire things up. Here's a shot of the floor frame of my 4x8' generator shed, built from 2x6 and 2x8 lumber, as well as the conduit running in a trench to the shed:

I had approximately 100 feet of distance from the generator shed to our main panel, where our electrician had wired us with an interlock and 100A breaker to backfeed into the panel. To keep the voltage drop down over this long run, I used 1/0 aluminum wire. Here's the junction where the 1/0 comes into the home and connects up to the 2-2-2-4 feeder wire that goes into the 100A interlock breaker in the main panel:

At the other end in the shed, the wiring would go into another breaker panel near the generator, and then transition to finely stranded copper wire (4 gauge) to connect to the generator itself. The finely stranded copper wire is required for its flexibility and vibration resistance, as aluminum would eventually fatigue and fracture if connected to a generator. Here's a shot of the 4-wire copper "mining" cable I used, connecting up to the generator head:

Connectors were "cold-weld" crimped onto this mining cable with a special hexagon crimp tool, which results in near-lossless connections. Similar crimps were used to transition the finely-stranded mining cable to coarse-stranded copper for the final run into the breaker panel in the shed (required because you cannot torque down finely-stranded copper in lugs):
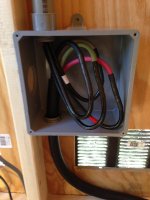
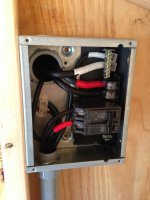
I planned to build the generator shed myself, but got tied up on a pier project that had a permit deadline. So I completed the floor and got the generator out there:

Then we hired one of the carpenters who worked on our home to build the shed to my specs, using similar materials and finishes from our home (main exception being we used T-111 siding on the shed instead of hardi-panel to keep costs down). He knocked out the shed in 4 days in did a great job:


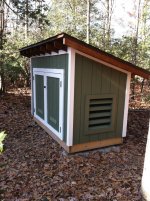
The shed has extensive venting between rafter tails to let warm air out, small intake vents down low, and two large louver vents -- one aligned with the radiator and its "pusher" fan, and the other in the opposite corner of the shed to provide makeup air. The shed also has a small door on the back to allow access to the battery, alternator, and starter.
The generator has a vertical muffler, and I got a custom tailpipe mandrel-bent so that I could route the exhaust up through a chimney in the roof:



For fuel, I am using a poly 55 gal drum (74 hours of runtime at 1/2 load). A duplex bushing (normally used for home heating oil tanks) attached to the bung on top and let me route a copper line down into the tank for a supply pickup and connect a return line:

I have a second 55 gal poly drum for reserve as needed. To bring fuel to the generator, I have a pallet-mounted 55 gal aluminum transfer tank with GPI hand pump that puts out a nice 0.5 gal per stroke, so refueling goes quickly. Here's a shot of me fueling up the tank the other night before we got hit with a snowstorm:

Finally, here are a couple movies of the generator running, with and without shed doors open:
https://vimeo.com/84737828
https://vimeo.com/84737847
Noise levels aren't too bad, but I plan to add some insulation to the shed to quiet things down a little more.
There are a lot of details I am not mentioning for brevity, so please feel free to ask questions! I should note that a local generator company quoted $10K for labor and materials to install a water-cooled generator (propane or diesel), which I initially scoffed at. But looking back and considering all the work I had to to for electrical, fuel, exhaust, mounting, etc, that $10K seems about right if I was paying someone typical trade labor rates. I saved a lot of money doing it myself, but it was a big project for sure.
thanks for reading,
219