BukitCase
Elite Member
- Joined
- Feb 17, 2012
- Messages
- 2,753
- Location
- Albany OR
- Tractor
- Case 580B, Long 460, Allis-Chalmers 160
Built this bending jig for use on my 20 ton press - all flat bar is 3/4 x 3, long dimension is 12", gap between uprights is 1/16" wider than the 1.5" male plunger plus two thicknesses of 1/2" x 3" bar stock -
The intent is to bend a couple of U-shaped 3" x 6" pieces of 1/2" mild steel by pushing them down between the two uprights.
It's only lightly tacked at present, and it's EXACTLY the size and shape I want it to be - hopefully when I'm done it won't explode when I try to cram a piece of 3" wide 1/2" flat bar into it
I'll be welding it out with my mm252 and .035 Lincoln L56 wire, C25 gas.
Question - would you preheat it (and if so, how hot) and weld it out hot then let it air cool, do small stitches and let cool between, fill the gap between left and right sides with solid bar stock and clamp in a vise and just go for it, or ??!?
I know it's tempting to voice opinions based on conjecture, but I'd prefer experience since I don't want to build another one of these just to get it right - it will only be used for sure on two un-even legged U-shaped pieces which will be the upper "hooks" of a quick-attach system for my Case 580's FEL. I want to be able to switch from bucket to grapple to hydraulic flail to forks to brush bucket without taking the whole day.
Thanks for any useful advice... Steve
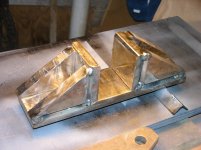
The intent is to bend a couple of U-shaped 3" x 6" pieces of 1/2" mild steel by pushing them down between the two uprights.
It's only lightly tacked at present, and it's EXACTLY the size and shape I want it to be - hopefully when I'm done it won't explode when I try to cram a piece of 3" wide 1/2" flat bar into it
I'll be welding it out with my mm252 and .035 Lincoln L56 wire, C25 gas.
Question - would you preheat it (and if so, how hot) and weld it out hot then let it air cool, do small stitches and let cool between, fill the gap between left and right sides with solid bar stock and clamp in a vise and just go for it, or ??!?
I know it's tempting to voice opinions based on conjecture, but I'd prefer experience since I don't want to build another one of these just to get it right - it will only be used for sure on two un-even legged U-shaped pieces which will be the upper "hooks" of a quick-attach system for my Case 580's FEL. I want to be able to switch from bucket to grapple to hydraulic flail to forks to brush bucket without taking the whole day.
Thanks for any useful advice... Steve

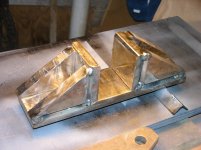