"I'm still having visual difficulty on where the welding machine is going, probably cause I cant see the side door in the pictures or maybe it's an invisible door and the trailer hitch cant quite see where which how that's going is either, I know you haven't made that movie yet. Pick point, now that's good planning.............PS Thanks for posting the pictures, looking like an awesome weld cart! "
I re-read my post, wasn't very clear - I was referring to the side door of the WELDER - didn't wanna hafta remove it from the cart to change wire, adjust tension, etc -
Positioning - check the first 4 pix on the first post of this thread, they are "pre-surgery" - as in, BEFORE I started "removing everything that isn't an elephant" (oops, I meant isn't a weld cart

)
Also, look close at this one
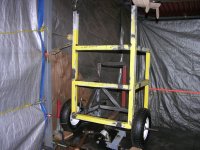
- it's marked where welder and bottle go; face of the welder will be angled up for better visibility, rear sets on that un-painted piece of angle at the back.
I'll add two "rails" along the sides of the welder (1" angle) so the welder can be positively strapped in place (Handtruck mode might get ugly otherwise) - Anywhere the welder touches the cart will get 1/4" neoprene glued in.
Also, because of the "offroad" options I didn't want the leads to be flopping around much, hence the dual hose hangers (no, they are NOT on wrong - mig gun will exit the welder front, wrap over the top of both, back around til it's almost all wrapped, then the gun goes in that piece of clamped on tubing (also used as a gun holder BETWEEN welds). Similar for ground and power leads: I typically plug in power, then ground, then gun, open gas, power up, set purge flow, go - so for shutdown, torch lead wraps first, then ground, then power.
Couple more pics, all I did today was set the axles for the 13" wheels and weld in place, clean up a bunch of flash rust, punch the hose hangers for mounting screws, weld a few tacked joints I'd missed - Tomorrow I need to cut out about 60% of the front middle cross-bar and reinforce what's left for bottle cage - that way there'll be room for a good-sized drawer under the welder that'll hold leathers, hood, gloves - and if it's tall enough, another Short drawer for nozzle gel, mig pliers, etc...
Trailer tongue will be 2 pieces - one piece will have FB on both sides, drilled for pivot and position pins, and will be welded to the underside of the frame - from center on the front to about 3" OUTSIDE of the rear bottom of frame. Second piece will have a hitch on outer end and will pin into the first piece. Both halves are 1-1/2"x.120" wall square tube. And you're right, the script for THAT movie is "still in re-write"

-
But in my head, the horizontal handle for the hand truck will get a sleeve that can move left-right to balance between welder and bottle, as well as one that slides front/back on a tube that'll connect the hand truck handle to the hitch end of the tongue when it's in vertical position. That should let me compensate for balance in BOTH directions so the picking eye will let it hang level. Both of those "leveling sleeves" will get set screws consisting of 5/8" dog pointed wing bolts for locking the sleeves to the picking frame parts.
Might get far enough tomorrow or the next day to set everything in place, then it oughta be clear as mudddd... Steve