OP
jschreib26
New member
Thanks for the continued help on this. Thanks to your help, I now understand the issue a bit more, but still am trying to get to the bottom of it: The jam which the bolt should hit is so far away from the bolt end that it would seemingly take an extremely tight turn to get near it. Long before it would get to that point, the wheel rubs against the loader upright. Though my turning radius would be greatly reduced, stopping the turn just at the point of wheel-to-loader contact still gives me enough to get around.
Also perhaps relevant is the fact that there is a mark where the bolt must have hit the jam at some point in the past, with a past owner. But that mark does not seem to be aligned with the current bolt placement?
Thinking I just needed a longer bolt, I got two (75mm) and put them in. Because they are just 10mm bolts I suspected they would bend or snap off. They did bend as soon as they hit the jam. The jam seems to be at an angle; the bolt doesn't hit it straight on.
So now a question: are there bolts of this size that might be hardened to the point that they would not bend? Why would the current bolt be so far from the jam? Because I use the loader daily, I can't really take it off, and so am hoping for the bolt fix. I can use the tractor now (and will be needing to use it a lot soon, if winter ever ends!) but cannot stay constantly focused on not turning the wheel too far -- I'll probably ruin the wheels, or worse, in no time. Note: the bolt in the attached pic is the old, shorter bolt.
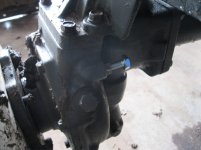
Also perhaps relevant is the fact that there is a mark where the bolt must have hit the jam at some point in the past, with a past owner. But that mark does not seem to be aligned with the current bolt placement?
Thinking I just needed a longer bolt, I got two (75mm) and put them in. Because they are just 10mm bolts I suspected they would bend or snap off. They did bend as soon as they hit the jam. The jam seems to be at an angle; the bolt doesn't hit it straight on.
So now a question: are there bolts of this size that might be hardened to the point that they would not bend? Why would the current bolt be so far from the jam? Because I use the loader daily, I can't really take it off, and so am hoping for the bolt fix. I can use the tractor now (and will be needing to use it a lot soon, if winter ever ends!) but cannot stay constantly focused on not turning the wheel too far -- I'll probably ruin the wheels, or worse, in no time. Note: the bolt in the attached pic is the old, shorter bolt.
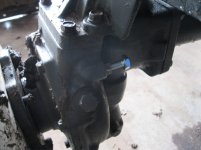