Now, the radiator.
First off-it was a wreck. But, no suitable replacement could easily be located, so my local radiator guy patched it back together as best as he could. here it is after he got done with it-
The factory shroud was long gone by the time I got this, so I decided seeing as I was making a career out of this tractor, I may as well build a new shroud. That and it gets hot here-the last thing I need is an overheating motor.
So, the first step was to take some heavy card paper and cut it to the proper size, then punch out bolt holes and bolt it to the radiator-
The lines are reference lines that I use to measure. More on that in a sec. Then, I bolt it up and mark out where the fan is in relation to the radiator. This one is tricky, as the fan is not fixed-to tighten the fan belt, the fan moves. The two different circles represent the two extreme locations of the blades-
That gives me a baseline idea of where the fan will be, but to get a more accurate measurement, I really need to know where the exact center of the fan is in its different positions, so I deployed my secret weapon-a Sharpie cut down and carefully taped up to the proper diameter and then inserted into the pilot hub for the fan-
So, back to those lines and measurements. Off of one point on the paper template, i use a square and graph out an X/Y coordinate map of all the points on the template. Then I put those points into my rusty-trusty computer, draw a bunch of other computer shapes, scratch my head a bunch, and then turn loose my favorite tool-well, favorite tool other than my beer bottle opener!-
Then a bunch of careful bending, careless swearing, and welding and a fan shroud begins to finally take shape. This is a two piece design, which is how I always make them-SOOOOOO much easier to work on!-
And here it is nearly complete and ready to bolt in the tractor and final fit-
Now, the original design had the radiator bolted by the bottom to the tractor frame with a few rubber washers, and the top was solid mounted with some rather poor brackets to the top of the tractor frame. A poor design and a recipe for disaster. In off-road applications, and most on road ones for that matter, you need to allow the radiator to move and float just a little to keep chassis flexing from fatiguing the radiator to death. The half-solid half rubber factory abortion may explain why the radiator was so hammered. So I added rubber bushings all the way around and beefed up the shroud in such a way as to keep the stress out of the radiator itself as much as possible. Here is one of the upper mounts tacked into place-
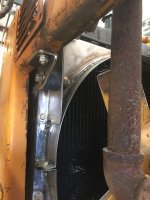