Teikas Dad
Gold Member
Getting ready to start welding things on the bucket of the tractor, but I haven't really welded anything in a couple years. I'm going to weld a length of 3/16" angle on the back of the bucket lip, then weld hooks and clevis mounts to that.
Before I screw up my bucket I figured it would be smart to do some practice runs.
I got some scrap pieces of 3/16 to keep everything the same and a couple extra hooks for a practice run. Running a Hobart HH187 with solid .35 wire and argon/co2 mix.
According to the chart (it's a tap machine so voltage/speed are machine settings), for 3/16 with AR/CO2 and .35 wire, the wire speed should be set at 50 and the voltage at 6 (out of 7). I kinda figured out the wire speed to the tap setting using simple math. The machine has settings from 10 to 100 for wire speed. The minimum speed on the unit is 40 IPM and max is 700 IPM, so hopefully my math was correct.
WS 10 20 30 40 50 60 70 80 90 100
IPM 40 114 187 260 334 407 480 553 627 700
Apparently the voltage is a sliding scale because it's effected by the wire speed. But, I calculated this out. The machine has settings from 1 to 7.
Setting 1 2 3 4 5 6 7
Voltage 13 19 21 23 25 27 30
Based on the settings it looks like the initial setup is 27 volts and 334 IPM. I ran a bead at that setting and I thought it was kind of thin. I upped the WS to 60 (407 IPM) and left the voltage on setting 6. That bead seemed to run pretty good. I figured I'd jack up the WS to 70 (480 IPM) and see what happened. The bead ran OK but it seemed to stick up more in the center compared to the WS of 60. The WS setting of 60 sounded the best too. It wasn't popping, sputtering or crackling, it was more of a steady sizzle/hum.
Here's what the three test beads look like:
I ran some more beads at the 60 and 70 settings, leaving the voltage on 6.
Sorry, camera took some crappy pictures.....
Here's a lap at 60.
I ran a bunch more practice beads to get back in the swing of things.
Eventually I took a shot at welding one of the hooks to a flat piece of 3/16 scrap.
Finally I took one of the hooks that are going on the bucket. This one is going on the back of the bucket just above the heel so I can lift with the bucket back if need be. The hook was welded to a 1/4" plate that I got from Ken's Bolt-on's.
This is the 1"X2" shackle mount that's going inside the bucket lip top. Also welded to one of Ken's plates.
Am I close enough for government work? Any comments, suggestions, advice or criticism is welcome and requested!
I found that I had to concentrate on not moving too fast. I also found out that I need some better cheater glasses under my helmet. The ones I have work good for the computer but not so good for welding, not strong enough. I did try out my new Hobart AD hood today and I'm very happy with it. I replaced a $50 Northern Tool AD helmet that I've had kicking around for 7 or 8 years.
Before I screw up my bucket I figured it would be smart to do some practice runs.
I got some scrap pieces of 3/16 to keep everything the same and a couple extra hooks for a practice run. Running a Hobart HH187 with solid .35 wire and argon/co2 mix.
According to the chart (it's a tap machine so voltage/speed are machine settings), for 3/16 with AR/CO2 and .35 wire, the wire speed should be set at 50 and the voltage at 6 (out of 7). I kinda figured out the wire speed to the tap setting using simple math. The machine has settings from 10 to 100 for wire speed. The minimum speed on the unit is 40 IPM and max is 700 IPM, so hopefully my math was correct.
WS 10 20 30 40 50 60 70 80 90 100
IPM 40 114 187 260 334 407 480 553 627 700
Apparently the voltage is a sliding scale because it's effected by the wire speed. But, I calculated this out. The machine has settings from 1 to 7.
Setting 1 2 3 4 5 6 7
Voltage 13 19 21 23 25 27 30
Based on the settings it looks like the initial setup is 27 volts and 334 IPM. I ran a bead at that setting and I thought it was kind of thin. I upped the WS to 60 (407 IPM) and left the voltage on setting 6. That bead seemed to run pretty good. I figured I'd jack up the WS to 70 (480 IPM) and see what happened. The bead ran OK but it seemed to stick up more in the center compared to the WS of 60. The WS setting of 60 sounded the best too. It wasn't popping, sputtering or crackling, it was more of a steady sizzle/hum.
Here's what the three test beads look like:
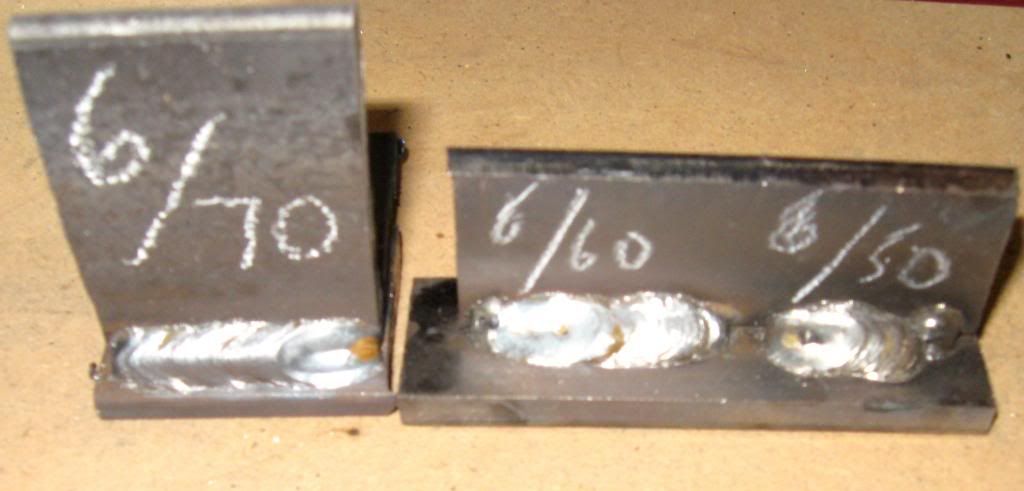
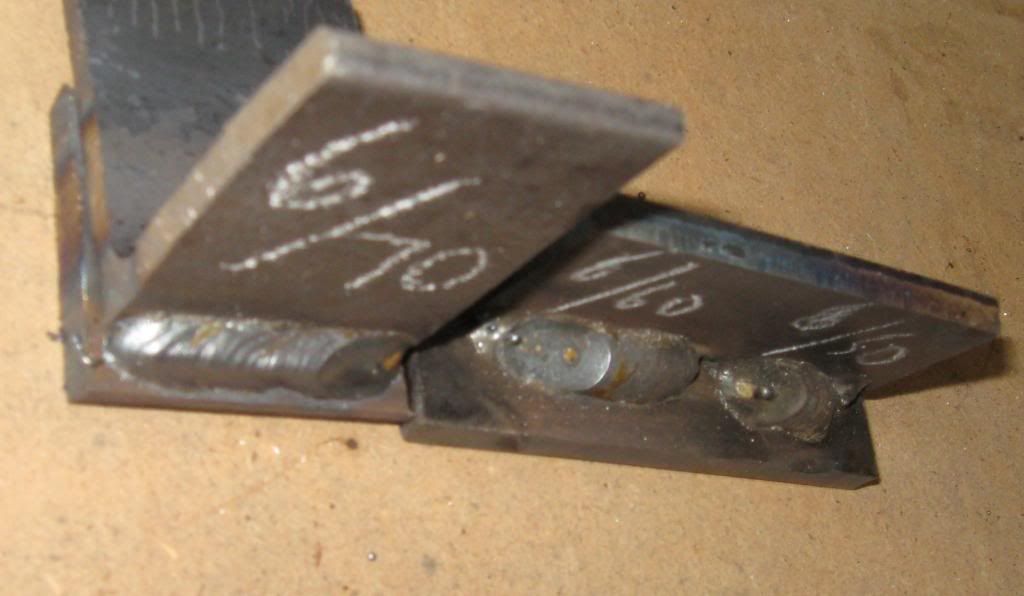
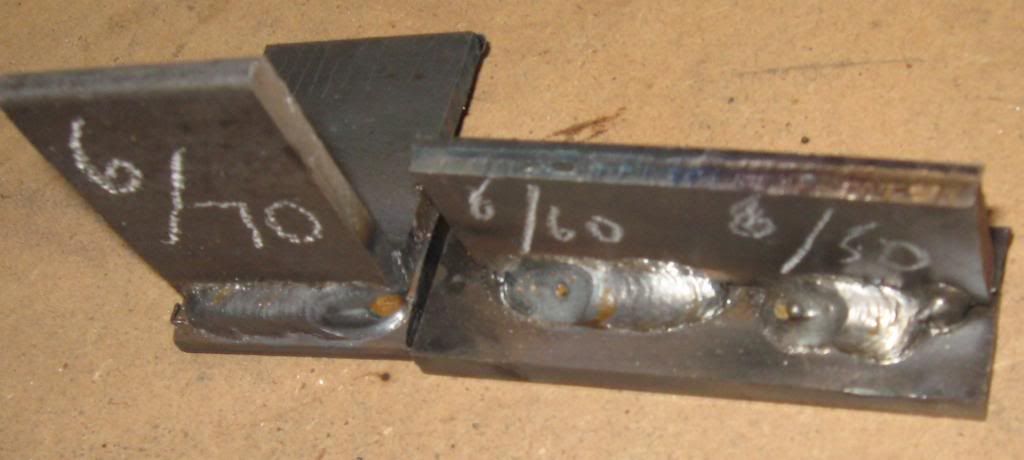
I ran some more beads at the 60 and 70 settings, leaving the voltage on 6.
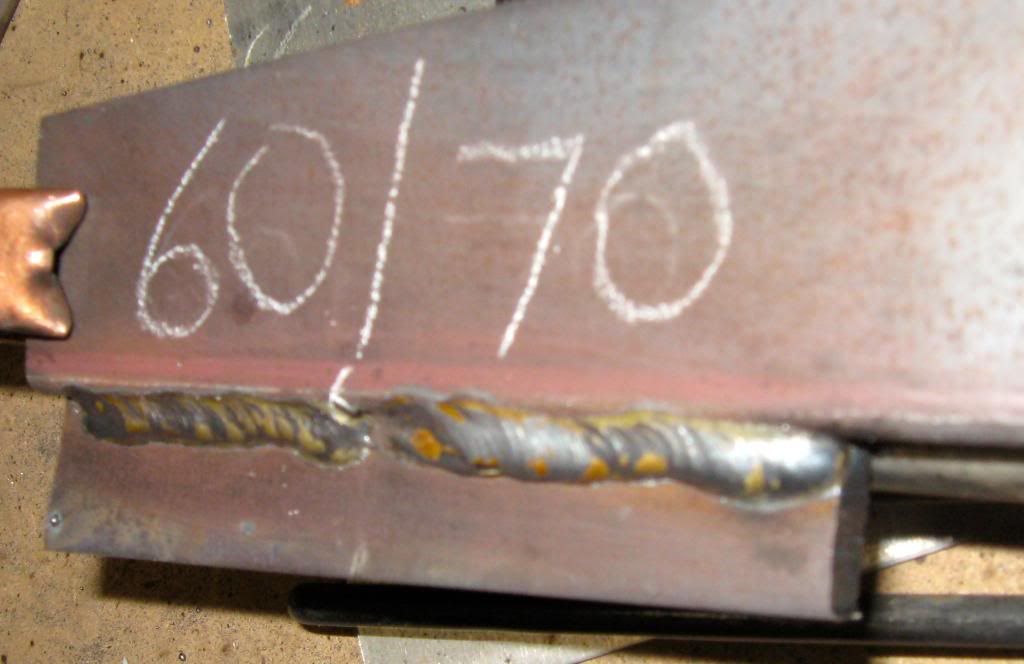
Sorry, camera took some crappy pictures.....
Here's a lap at 60.
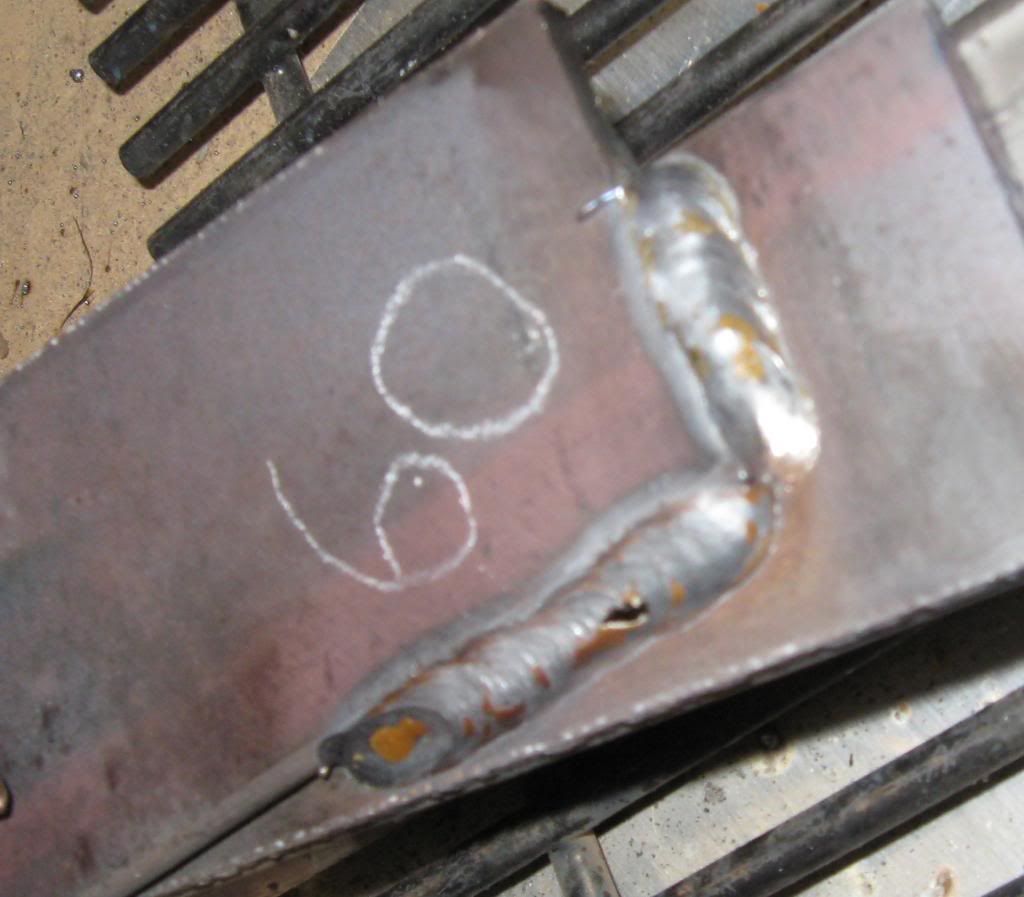
I ran a bunch more practice beads to get back in the swing of things.
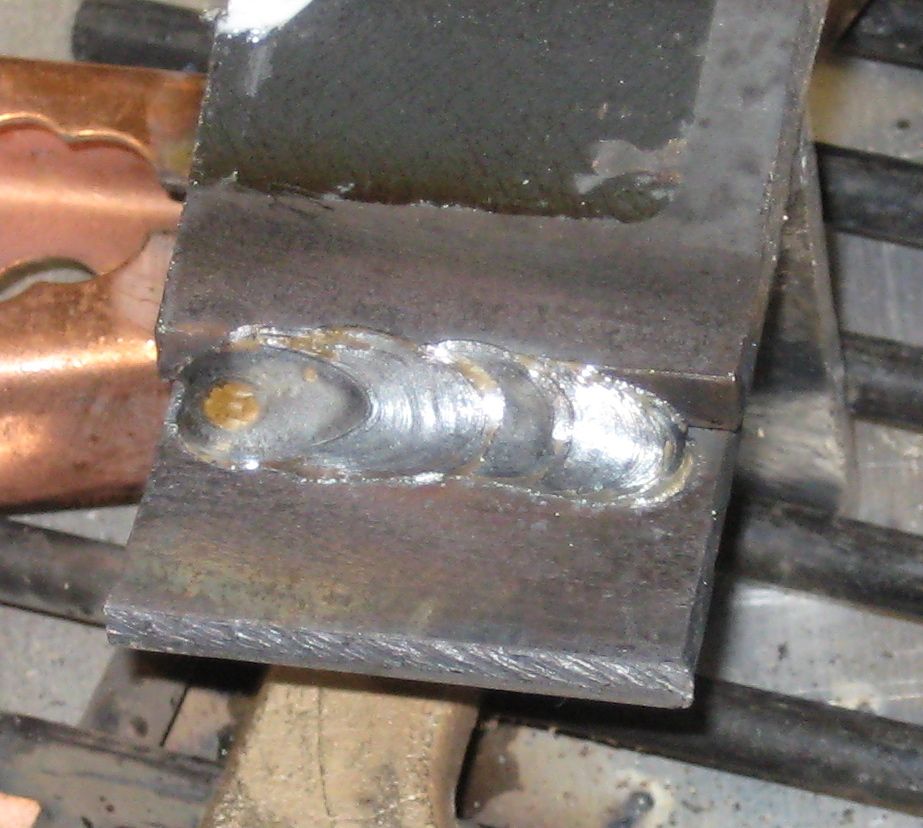
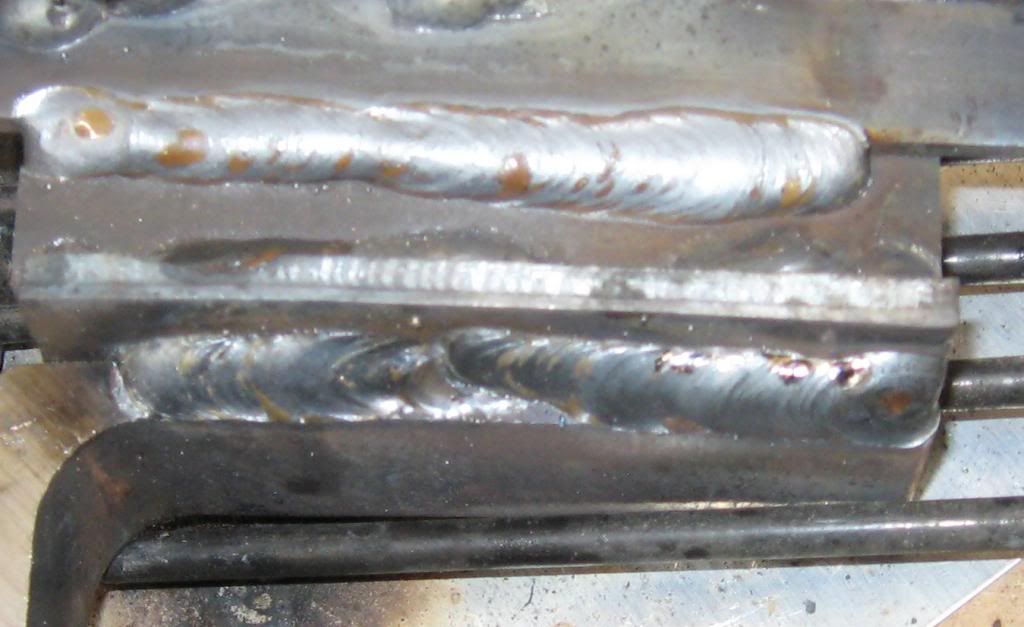
Eventually I took a shot at welding one of the hooks to a flat piece of 3/16 scrap.
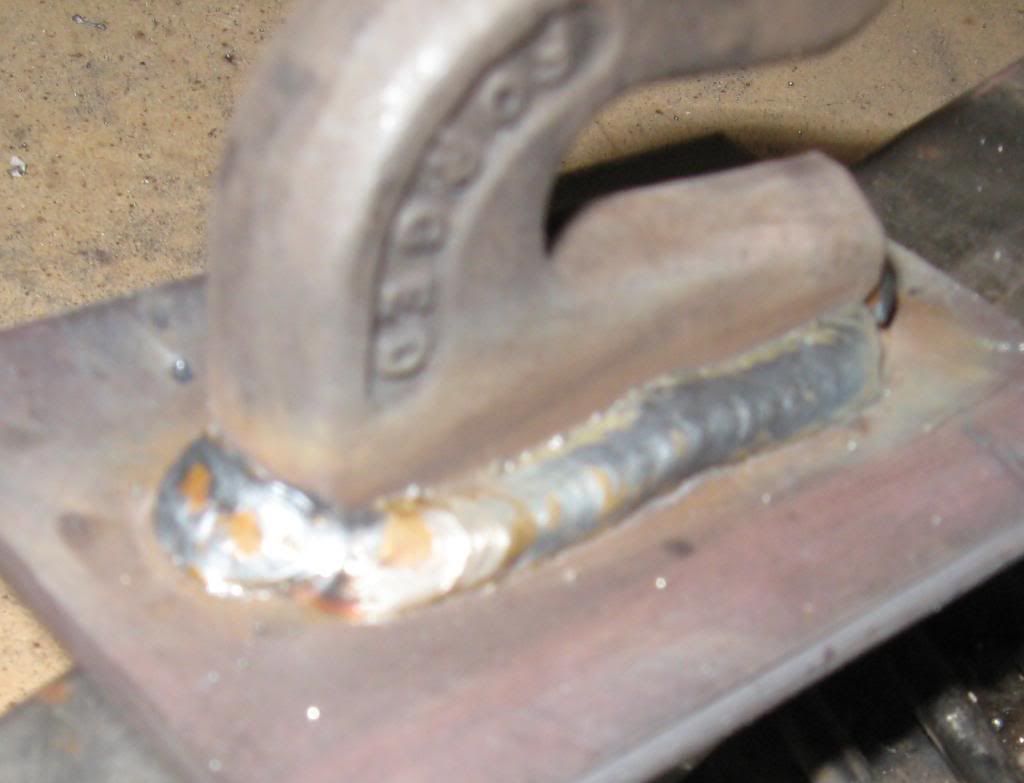
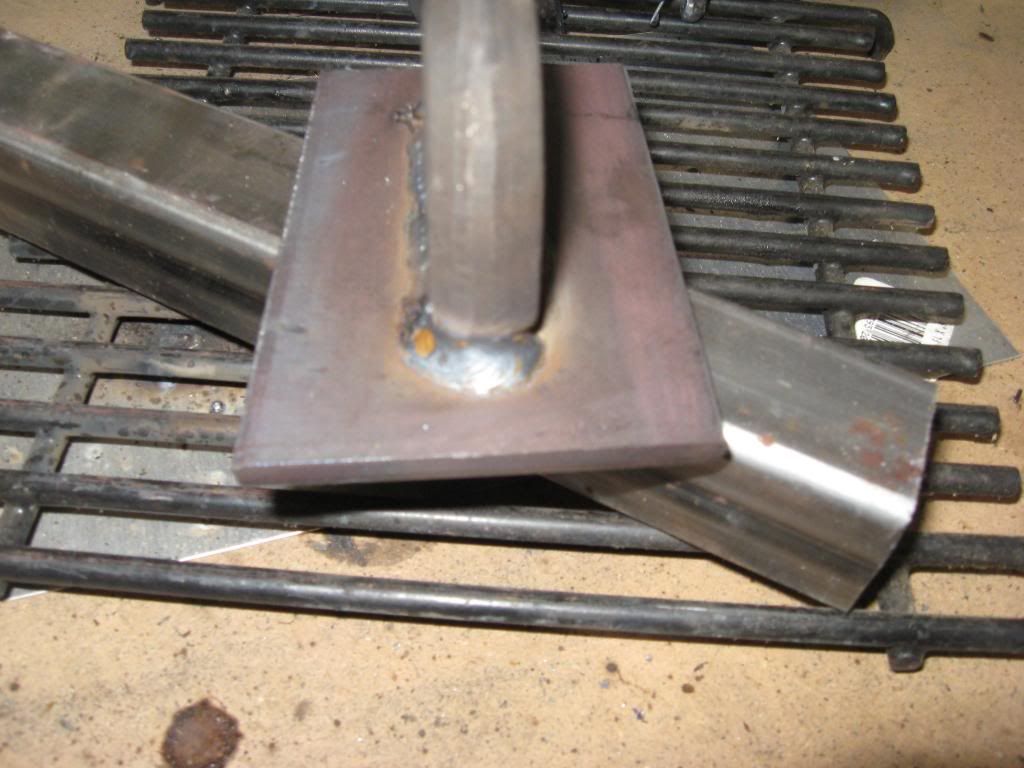
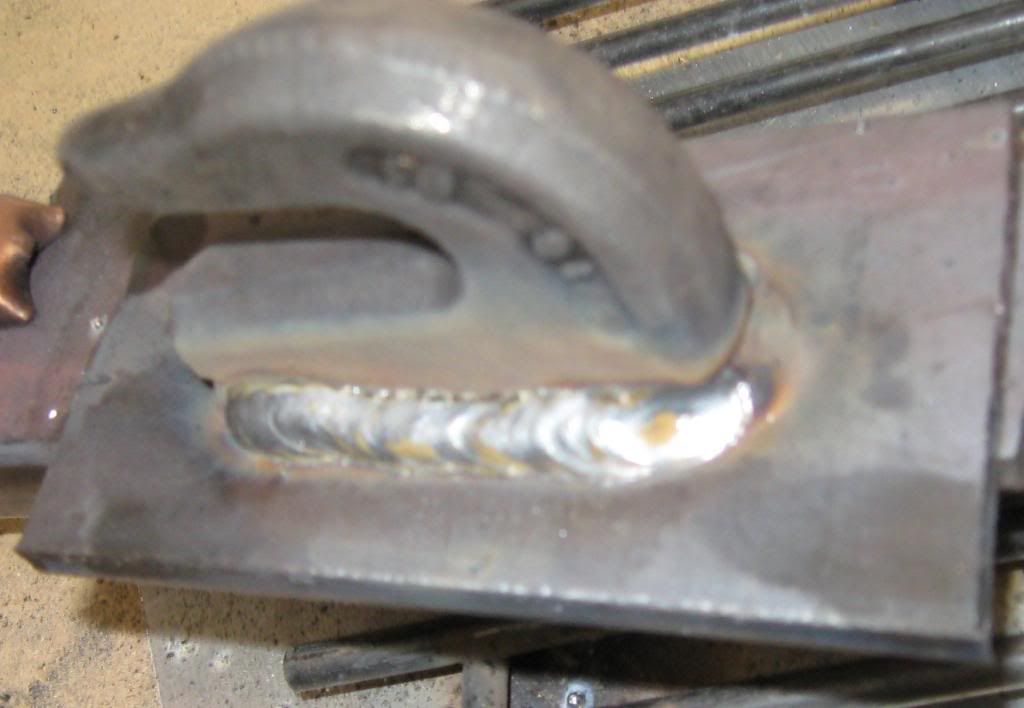
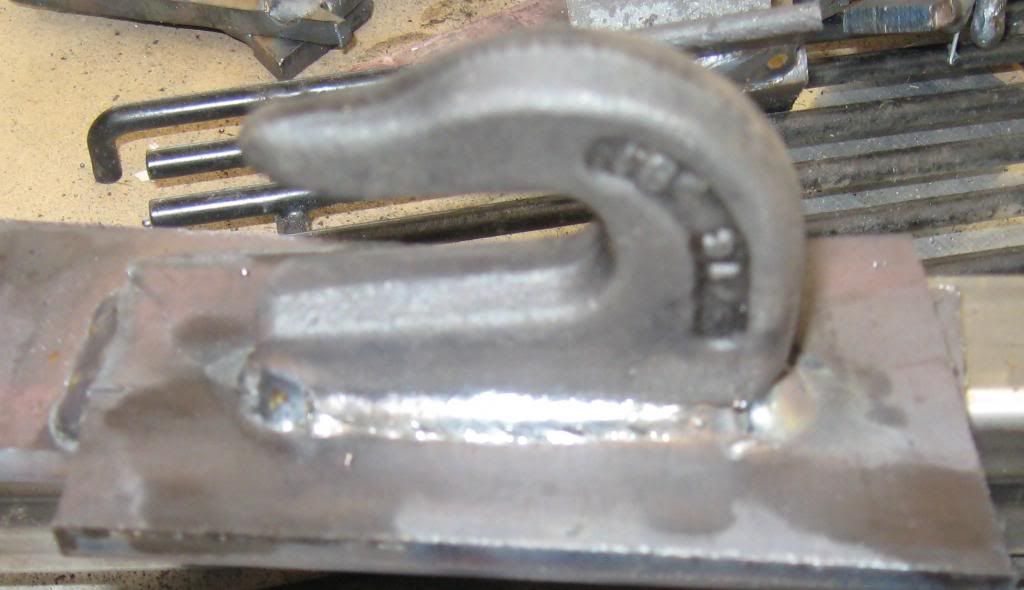
Finally I took one of the hooks that are going on the bucket. This one is going on the back of the bucket just above the heel so I can lift with the bucket back if need be. The hook was welded to a 1/4" plate that I got from Ken's Bolt-on's.
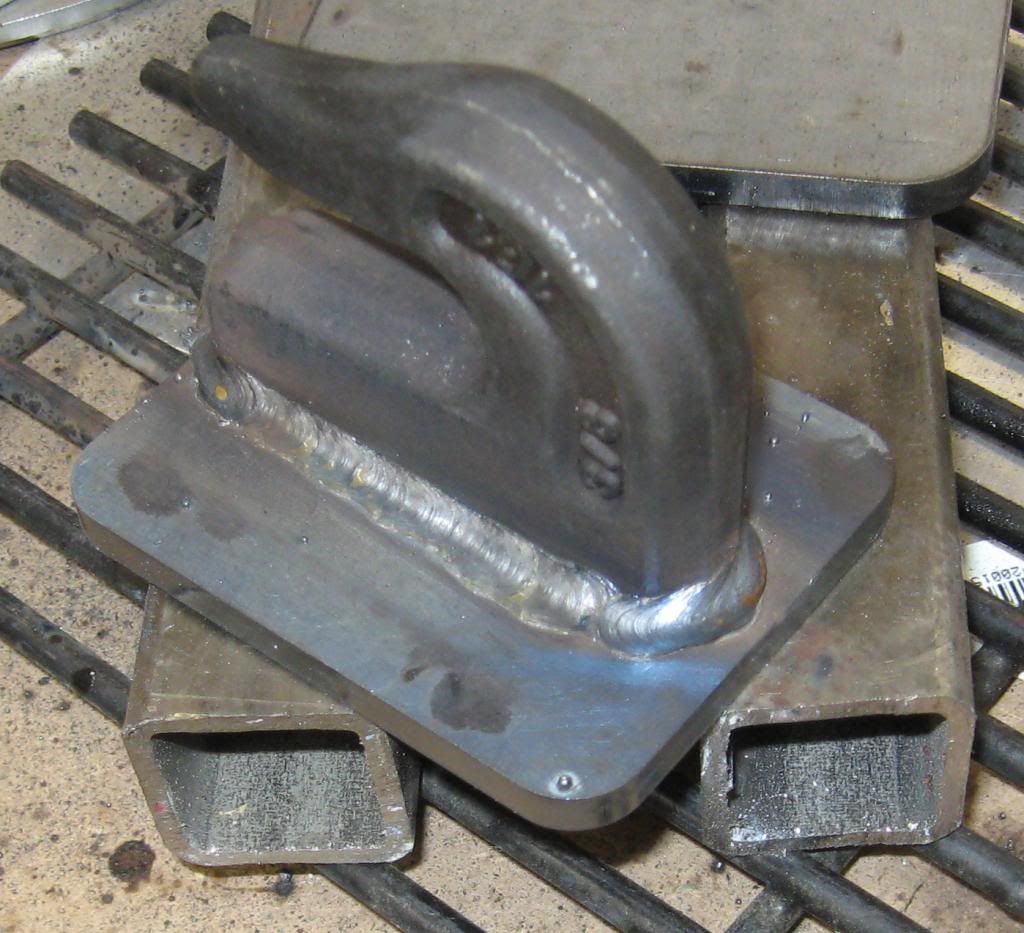
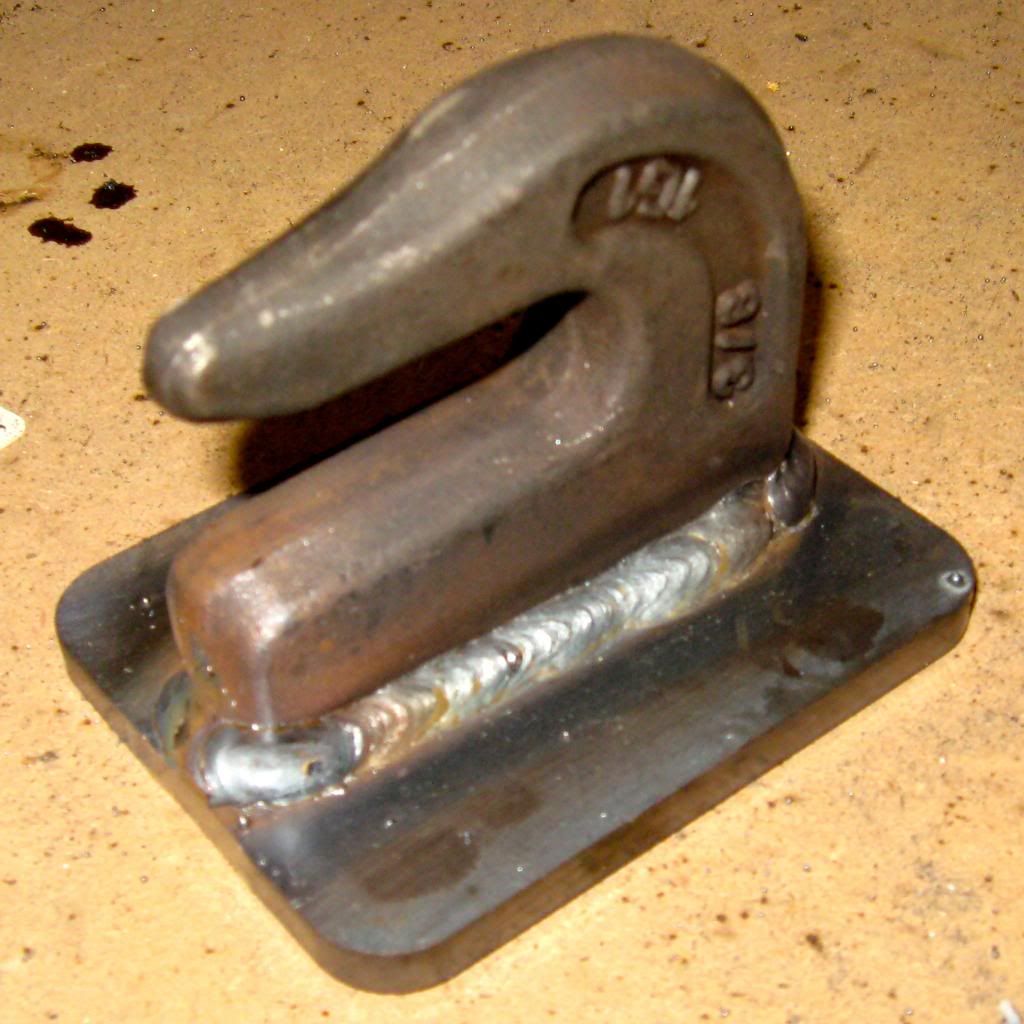
This is the 1"X2" shackle mount that's going inside the bucket lip top. Also welded to one of Ken's plates.
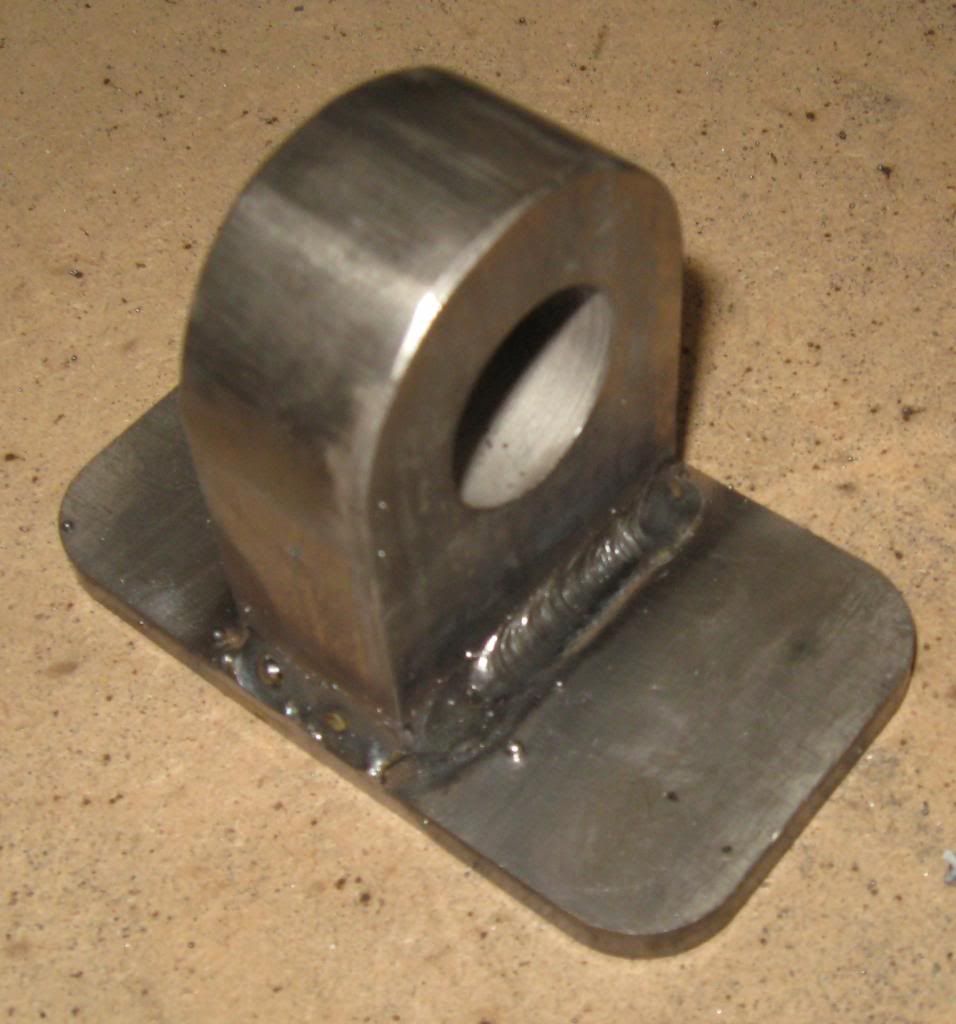
Am I close enough for government work? Any comments, suggestions, advice or criticism is welcome and requested!
I found that I had to concentrate on not moving too fast. I also found out that I need some better cheater glasses under my helmet. The ones I have work good for the computer but not so good for welding, not strong enough. I did try out my new Hobart AD hood today and I'm very happy with it. I replaced a $50 Northern Tool AD helmet that I've had kicking around for 7 or 8 years.