lennyzx11
Veteran Member
- Joined
- Dec 20, 2015
- Messages
- 1,255
- Location
- Bennington Vermont
- Tractor
- Kubota L3301 HST/LA525 & 1964 Ford 2000 gas
After starting to make a thumb for my Woods 7500, I noticed that Titan had a weld it kit for a 24” pin type. For 140 bucks. Hard to buy the metal for much less.
DIY 24" Weld On Backhoe Thumb Hoe Clamp .5" Steel Plate Assembly CNC Plasma Cut
It came in a sturdy well wrapped package. That was heavy at 60 lbs.
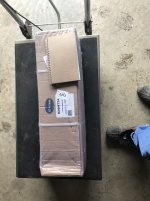

1/4” steel throughout and the holes were close enough with a little grinding to be done to mate everything up properly. Chinese tolerances you know.
Then I noticed that no matter which way I Tried to do it, it wouldn’t fold down to the boom.
The geometry appears wrong in the hole placements.

In the above picture, the backbone is laying down on its back, the brace is inside and one jaw close toward camera.
The three holes are aligned in the backbone and brace have pins in them. The one hole toward the middle does not have a corresponding hole in the brace inside the backbone.
The two holes line up in the jaw and backbone but not the brace.
Trying to fold it together the way you would think leaves two end holes blocked by the jaws not allowing a pin to be inserted for storage.

This shows the jaw on the far side blocking the two holes in the backbone. With the brace ready to fold down inside.
The easiest way to get something that will fold up to me is to drill two holes in the brace to mate with the middle set holes in the jaws and backbone I think.
Drilling to match the jaws to the other holes on the tips would compromise their strength I believe.
Trouble is, my way I think it will be a PITA from now on to unfold and fold because of having pins through all 3 pieces that have to be removed means you get to juggle the jaws and brace in your hands all at the same time as no one pin can be left in place to unfold and pivot on.
Thinking of cutting one end of the brace off to shorten it or drilling another hole in the brace to offset it away from one end. This would allow one pin through the jaws and backbone to remain as the pivot all the time.
I’m in the “pondering “ mode for a bit before I weld it all together or bore holes in 1/4” steel.
Open to thoughts from the brain trust.
Lenny
DIY 24" Weld On Backhoe Thumb Hoe Clamp .5" Steel Plate Assembly CNC Plasma Cut
It came in a sturdy well wrapped package. That was heavy at 60 lbs.
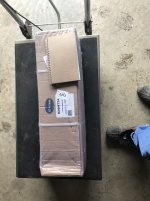

1/4” steel throughout and the holes were close enough with a little grinding to be done to mate everything up properly. Chinese tolerances you know.
Then I noticed that no matter which way I Tried to do it, it wouldn’t fold down to the boom.
The geometry appears wrong in the hole placements.

In the above picture, the backbone is laying down on its back, the brace is inside and one jaw close toward camera.
The three holes are aligned in the backbone and brace have pins in them. The one hole toward the middle does not have a corresponding hole in the brace inside the backbone.
The two holes line up in the jaw and backbone but not the brace.
Trying to fold it together the way you would think leaves two end holes blocked by the jaws not allowing a pin to be inserted for storage.

This shows the jaw on the far side blocking the two holes in the backbone. With the brace ready to fold down inside.
The easiest way to get something that will fold up to me is to drill two holes in the brace to mate with the middle set holes in the jaws and backbone I think.

Drilling to match the jaws to the other holes on the tips would compromise their strength I believe.
Trouble is, my way I think it will be a PITA from now on to unfold and fold because of having pins through all 3 pieces that have to be removed means you get to juggle the jaws and brace in your hands all at the same time as no one pin can be left in place to unfold and pivot on.
Thinking of cutting one end of the brace off to shorten it or drilling another hole in the brace to offset it away from one end. This would allow one pin through the jaws and backbone to remain as the pivot all the time.
I’m in the “pondering “ mode for a bit before I weld it all together or bore holes in 1/4” steel.
Open to thoughts from the brain trust.
Lenny