erkme73
Silver Member
Right up front, let me say this is operator error. I did not know checking the loader bracket bolts was something to do - but will from now on. After having been told by several internet folk I should have RTFM, I did just that, but found no specific reference to the loader bracket bolts, or what their torque values should be.
In any case, I had the two front-most bolts (M14 x 2.0, 10.9 grade) bolts shear off on the right side, and one shear off on the left (with the remaining bolt loose and damaged). I had noticed some "slop" in the FEL the last couple of uses, but didn't notice the missing/loose bolts. The last time I used it, I heard a snap and a "ting" as some thing metal shot out across the gravel. I stopped everything and searched until I found the problem.


On the first one, I attempted to remove it using a bolt extractor. I worked my way up to the largest (#6) but still was unable to get the bolt to budge. With the hole for the extractor being slightly off center, and getting close to the hole wall, I opted to drill the hole out to the M14 diameter and tap it out for the M14x2.0 bolt. Surprisingly that worked well. Lots of swearing and sweating bullets (I did not want to snap off the tap inside my new hole), but it worked. I ran the tap through the other hole on the same side to clean it up since the original bolt was galled up a bit from being loose.
Today I moved to the other side. After several others (including dealer tech) suggested welding a nut on what was left of the bolt, I did just that. The first (lower) bolt took two tries, but I was able to gently coax the bolt out of the hole:
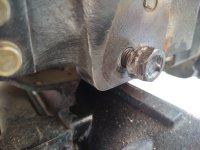
I then attempted the same approach on the top bolt. After 6 attempts, it was clear the weld was not strong enough to overcome the rust/corrosion on the threads. So I opted to drill the bolt out to re-tap as I had done on the other side. This was a mistake. Focused more on applying the correct pressure, I did not notice that the drill bit was walking away from the initial hole. By the time I realized it, I had a hole that was well off target, and oblong. Very frustrated with myself, and I'm now going to sleep on it (while licking my wounds). I have a several professional welder friends that have recommended filling the hole with 6010 electrode and redrilling/tapping. I will probably give that a go - maybe even have them come do it for me.
For now, I've reassembled with 3 fully torqued bolts (albeit they're only grade 8.8 as no one had 10.9 in the correct size over the weekend) as place-holders. Tomorrow, I'll hit a Fastenal to get the correct bolts... And see what they recommend for the fix.
As embarrassing as it is, here's is my wonderful hack-job... go easy on me.
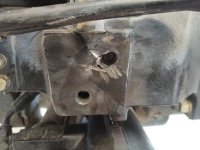
Incidentally, I have looked everywhere to find the torque specs for the loader bracket. There are 4 long main bolts on the right bracket, and 5 on the left. They were all extremely tight, and required the impact wrench to get them all the way out. The threads are all quite rusted/corroded at the point where they were in the frame. Dissimilar metal oxidation perhaps?
In any case, I've maxed them out on torque with my 1/2" drive pneumatic wrench (which is what the dealer tech recommended and said that's all they do), and I've painted lines on all bolts.
In any case, I had the two front-most bolts (M14 x 2.0, 10.9 grade) bolts shear off on the right side, and one shear off on the left (with the remaining bolt loose and damaged). I had noticed some "slop" in the FEL the last couple of uses, but didn't notice the missing/loose bolts. The last time I used it, I heard a snap and a "ting" as some thing metal shot out across the gravel. I stopped everything and searched until I found the problem.


On the first one, I attempted to remove it using a bolt extractor. I worked my way up to the largest (#6) but still was unable to get the bolt to budge. With the hole for the extractor being slightly off center, and getting close to the hole wall, I opted to drill the hole out to the M14 diameter and tap it out for the M14x2.0 bolt. Surprisingly that worked well. Lots of swearing and sweating bullets (I did not want to snap off the tap inside my new hole), but it worked. I ran the tap through the other hole on the same side to clean it up since the original bolt was galled up a bit from being loose.
Today I moved to the other side. After several others (including dealer tech) suggested welding a nut on what was left of the bolt, I did just that. The first (lower) bolt took two tries, but I was able to gently coax the bolt out of the hole:
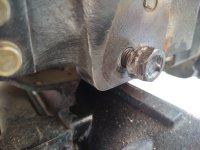
I then attempted the same approach on the top bolt. After 6 attempts, it was clear the weld was not strong enough to overcome the rust/corrosion on the threads. So I opted to drill the bolt out to re-tap as I had done on the other side. This was a mistake. Focused more on applying the correct pressure, I did not notice that the drill bit was walking away from the initial hole. By the time I realized it, I had a hole that was well off target, and oblong. Very frustrated with myself, and I'm now going to sleep on it (while licking my wounds). I have a several professional welder friends that have recommended filling the hole with 6010 electrode and redrilling/tapping. I will probably give that a go - maybe even have them come do it for me.
For now, I've reassembled with 3 fully torqued bolts (albeit they're only grade 8.8 as no one had 10.9 in the correct size over the weekend) as place-holders. Tomorrow, I'll hit a Fastenal to get the correct bolts... And see what they recommend for the fix.
As embarrassing as it is, here's is my wonderful hack-job... go easy on me.
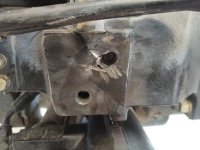
Incidentally, I have looked everywhere to find the torque specs for the loader bracket. There are 4 long main bolts on the right bracket, and 5 on the left. They were all extremely tight, and required the impact wrench to get them all the way out. The threads are all quite rusted/corroded at the point where they were in the frame. Dissimilar metal oxidation perhaps?
In any case, I've maxed them out on torque with my 1/2" drive pneumatic wrench (which is what the dealer tech recommended and said that's all they do), and I've painted lines on all bolts.