sequoyah101
Silver Member
- Joined
- Nov 13, 2009
- Messages
- 157
- Location
- East Central Oklahoma
- Tractor
- CaseIH 50A, CaseIH JX95, CaseIH JX80, Allis 190XT, Daewoo DD80L Dozer, Schaeff SKL831 Loader, Komatsu PC40-7 Trackhoe, JCB 210S TLB, JD750, JD820, Kubota FR3680, Kioti Mechron
After years of noodling on how to build a post driver I have finally done it and it works well enough to refine the design.
I considered all manner of designs from:
A. Reverse block and tackle with a hydraulic cylinder (Fairbrothers, et al type), don't like all the lines and moving parts and need for a big dump valve
B. Lever knocker (Parmiter, Protec and Vector types) all of which I really like because they are so compact to even fit on a backhoe or mini-excavator but the drop is limited though they do work well apparently. For long posts you have to hoist the entire mechanism and then lower it as the post is driven.
C. Two part line block and tackle with hydraulic cylinder (Fieldmaster or Malone type), nice and simple, reduced moving parts but still has need for a high flow dump line
D. Hydraulic motor and roller chain weight hoist and trip drop (Danuser and Cross type), nifty design, not hard to build, requires mast and big weight.
E. Vibratory such as plate compactors or the Danuser T3 that uses a hydraulic motor, cam and spring for a high frequency knocker.
F. I really wanted a demolition tool but too expensive even used and pretty heavy.
My design criteria were:
1. Drive up to 4.5" pipe, I don't care a whit about driving wood posts or railroad ties. They are a waste of time for building fence meant to last. Build it with steel, build it to last.
2. Drive pipe up to 12' long
3. Have a mast and post guide to keep things straight
4. Manage one-man operation in a pinch
5. Quick hitch primary carrier on loader with option to add to backhoe or midi-excavator
6. Easily adapted to side shift and tilt adjustments
7. Rock spike option
8. Prefer all operation from cab
9. Mast and associated mechanism adaptable to water well drilling rig.
Jackhammers were intriguing but all indications given by people I spoke to who had used them and the limitations on hydraulic post pounders used mostly for signage and "pin" drivers suggested high cost and limited capability. I continued to mull over my options even going so far as to begin acquiring lead for the drop weight. Lead being much better than just steel since it does not bounce so much. I liked the idea of the motor and chain trip hammer design and dismissed my favorite, the knocker type (option B above).
Hydraulic Jackhammers still called me but the used were $600 and up. One took a chance that they might not work well at all and if they did work, not work well enough for my mission. One day a deal came along too good to pass up. A Stanley BR72 Hydraulic Jackhammer, military surplus, apparently unused condition $200 bucks. Opportunity and my $200 bucks consummated the deal I now had a Jackhammer to try out. Brought it home, made up some new whips, got a 4.5" pipe section, something to stand on, made up sort of a driving head, ground off the point of a moll, held the hammer while my helper engaged the hydraulics on the tractor and the fight was on. The summer was dry and the ground harder than a *****'s heart but the hammer did work, sort of but very hard to control. I rigged down and parked the hammer in the corner of the barn. That was three years ago. I hired a welder and in the last three years he has built all manner of corners, brace panels, water crossings, a hay barn and so forth. He drove all the posts with an old Dansuer pto driver and a small JD tractor. All posts are at least 4' deep good job!
Here comes the CORONA virus and social distancing so I've tackled some things that have been just lying around waiting for attention. The Jackhammer is one of those things and so it began. I had a 3/8" skid steer plate and some 1/2" flat steel and some 3/8" x 4" x 4" I think angle iron, sketched out the plan on the welding table and started cutting steel. Pictured is what I built. It works like a wind shield wiper on a duck's butt, that means very well.
There was a little false start. I built a drive cup and using a bolt clamped it onto the cut off moll. In a test run I drove 2 7/8" pipe 5' deep and was going for 6' and below ground level until the drive cup broke while I was trying to straighten the pipe and bent the pipe as well. I suspected I was going to have to spring for a proper drive cup and during the time I was mulling over the whole Jackhammer thing I located just such a thing at Crowder Supply up in Colorado. They will even make custom drive cups for you if you have the money they have the ability. Some people say I'm cheap but I prefer extremely frugal. I try not to get confused about need and want and am a child of Depression era parents who didn't even have enough to eat sometimes. The Depression left an impression on us.
Anyway, a phone call for confirmation of dimensions, an online order and Paypal later I received my Crowder Supply 3" drive cup and detachable permanently driven into place shank for the limited time bargain price of $200 bucks, same thing I paid for the Jackhammer. It is a massive and beautifully turned chunk of steel reminding me of some of the stuff we ran in oil wells and never saw again. I digress.
With new drive pin and rig and cut to length 2 7/8" and 3" pipe I went out for a trial run. Put in four berry trellis posts 5' deep into as much hard clay as could be found and two 3" sleeves for the wife's new clothes line also driven 5' deep. The hammer is rated at 8 gpm and 1,300 blows per minute. I put the loader boom in float for added weight and let the tractor idle which means I was getting maybe 3 gpm and 500 bpm. My soil is wet and loamy sometimes for several feet but on the hill where the house is there is a layer of clay about 2 feet down with cobbles in it. 3" pipe sails down all the way.
The hammer was new but unused and probably more than 20 years old. All hydraulic seals get old and brittle and leak with use and these do now so I am shut down until I can get a seal kit and nitrogen charge kit. Seal replacement is field service and you would think Stanley would be able to build a charge kit for less than $600. The hammer charge service kits on Ebay are reasonable but I'm not sure of the threads for the charge port. I hope that low cost alternative works out.
Some say a drop hammer is faster than a hydraulic hammer or vibratory post driver. These are the people who make drop hammers. I calculated the energy of a 500 lb drop hammer falling about 6' and one blow every 10 seconds generates about 300 ft-lbs/min of work or about 0.009 hp. My Jackhammer with just self-weight and 1,300 bpm produces 93,600 ft-lbs/min of work or about 2.8 hp. Skildril makes a hydraulic post driver that puts out 4.2 hp and 138,000 ft-lbs/min. Seems like the hydraulic hammer should be faster than the drop hammer and more controllable.
Lots of outfits make hydraulic, electric and air jackhammers. The Bosch Brute is electric and generates about 1.5 hp as an example
Next I'll repair the hammer, figure out how to charge it and build a mast with a roller chain hydraulic motor hoist and post holding fixture to keep things straight. I'll also make a larger drive cup attachment to clamp on to this one using a chunk of 1" plate and some proper sized pipe. I'm a little concerned about not having enough weight with the mast but I have a few sections of mainline rail I can strap on to the hammer carrier. As for water well drilling, I'll use the hydraulic post hole auger head, a fluid swivel and centrifugal pump. On the Gulf Coast I used 1" NPT pipe with stops to keep from driving the pins through the couplings. Where I am now I'll need to invest in some rotary shouldered drill pipe. For driving pipe up to 8' long I don't really need a mast but it would be neat. Without a mast for longer pipe all you need to do is weld on a section at a time.
So far I am pleased but disappointed that the hydraulic seals failed so soon and that the nitrogen charge kit is stupid money expensive. At the end of the day I have not built much but instead made what I believe is a successful adaptation.
I guess I've attached these pictures correctly. You can see that my shop helper isn't too work brittle. He just never takes anything seriously.
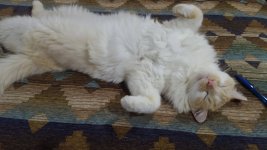
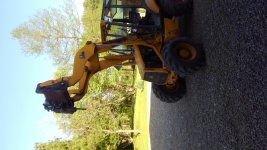
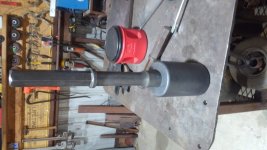
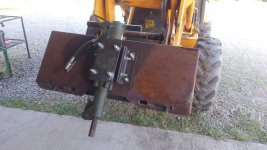
I considered all manner of designs from:
A. Reverse block and tackle with a hydraulic cylinder (Fairbrothers, et al type), don't like all the lines and moving parts and need for a big dump valve
B. Lever knocker (Parmiter, Protec and Vector types) all of which I really like because they are so compact to even fit on a backhoe or mini-excavator but the drop is limited though they do work well apparently. For long posts you have to hoist the entire mechanism and then lower it as the post is driven.
C. Two part line block and tackle with hydraulic cylinder (Fieldmaster or Malone type), nice and simple, reduced moving parts but still has need for a high flow dump line
D. Hydraulic motor and roller chain weight hoist and trip drop (Danuser and Cross type), nifty design, not hard to build, requires mast and big weight.
E. Vibratory such as plate compactors or the Danuser T3 that uses a hydraulic motor, cam and spring for a high frequency knocker.
F. I really wanted a demolition tool but too expensive even used and pretty heavy.
My design criteria were:
1. Drive up to 4.5" pipe, I don't care a whit about driving wood posts or railroad ties. They are a waste of time for building fence meant to last. Build it with steel, build it to last.
2. Drive pipe up to 12' long
3. Have a mast and post guide to keep things straight
4. Manage one-man operation in a pinch
5. Quick hitch primary carrier on loader with option to add to backhoe or midi-excavator
6. Easily adapted to side shift and tilt adjustments
7. Rock spike option
8. Prefer all operation from cab
9. Mast and associated mechanism adaptable to water well drilling rig.
Jackhammers were intriguing but all indications given by people I spoke to who had used them and the limitations on hydraulic post pounders used mostly for signage and "pin" drivers suggested high cost and limited capability. I continued to mull over my options even going so far as to begin acquiring lead for the drop weight. Lead being much better than just steel since it does not bounce so much. I liked the idea of the motor and chain trip hammer design and dismissed my favorite, the knocker type (option B above).
Hydraulic Jackhammers still called me but the used were $600 and up. One took a chance that they might not work well at all and if they did work, not work well enough for my mission. One day a deal came along too good to pass up. A Stanley BR72 Hydraulic Jackhammer, military surplus, apparently unused condition $200 bucks. Opportunity and my $200 bucks consummated the deal I now had a Jackhammer to try out. Brought it home, made up some new whips, got a 4.5" pipe section, something to stand on, made up sort of a driving head, ground off the point of a moll, held the hammer while my helper engaged the hydraulics on the tractor and the fight was on. The summer was dry and the ground harder than a *****'s heart but the hammer did work, sort of but very hard to control. I rigged down and parked the hammer in the corner of the barn. That was three years ago. I hired a welder and in the last three years he has built all manner of corners, brace panels, water crossings, a hay barn and so forth. He drove all the posts with an old Dansuer pto driver and a small JD tractor. All posts are at least 4' deep good job!
Here comes the CORONA virus and social distancing so I've tackled some things that have been just lying around waiting for attention. The Jackhammer is one of those things and so it began. I had a 3/8" skid steer plate and some 1/2" flat steel and some 3/8" x 4" x 4" I think angle iron, sketched out the plan on the welding table and started cutting steel. Pictured is what I built. It works like a wind shield wiper on a duck's butt, that means very well.
There was a little false start. I built a drive cup and using a bolt clamped it onto the cut off moll. In a test run I drove 2 7/8" pipe 5' deep and was going for 6' and below ground level until the drive cup broke while I was trying to straighten the pipe and bent the pipe as well. I suspected I was going to have to spring for a proper drive cup and during the time I was mulling over the whole Jackhammer thing I located just such a thing at Crowder Supply up in Colorado. They will even make custom drive cups for you if you have the money they have the ability. Some people say I'm cheap but I prefer extremely frugal. I try not to get confused about need and want and am a child of Depression era parents who didn't even have enough to eat sometimes. The Depression left an impression on us.
Anyway, a phone call for confirmation of dimensions, an online order and Paypal later I received my Crowder Supply 3" drive cup and detachable permanently driven into place shank for the limited time bargain price of $200 bucks, same thing I paid for the Jackhammer. It is a massive and beautifully turned chunk of steel reminding me of some of the stuff we ran in oil wells and never saw again. I digress.
With new drive pin and rig and cut to length 2 7/8" and 3" pipe I went out for a trial run. Put in four berry trellis posts 5' deep into as much hard clay as could be found and two 3" sleeves for the wife's new clothes line also driven 5' deep. The hammer is rated at 8 gpm and 1,300 blows per minute. I put the loader boom in float for added weight and let the tractor idle which means I was getting maybe 3 gpm and 500 bpm. My soil is wet and loamy sometimes for several feet but on the hill where the house is there is a layer of clay about 2 feet down with cobbles in it. 3" pipe sails down all the way.
The hammer was new but unused and probably more than 20 years old. All hydraulic seals get old and brittle and leak with use and these do now so I am shut down until I can get a seal kit and nitrogen charge kit. Seal replacement is field service and you would think Stanley would be able to build a charge kit for less than $600. The hammer charge service kits on Ebay are reasonable but I'm not sure of the threads for the charge port. I hope that low cost alternative works out.
Some say a drop hammer is faster than a hydraulic hammer or vibratory post driver. These are the people who make drop hammers. I calculated the energy of a 500 lb drop hammer falling about 6' and one blow every 10 seconds generates about 300 ft-lbs/min of work or about 0.009 hp. My Jackhammer with just self-weight and 1,300 bpm produces 93,600 ft-lbs/min of work or about 2.8 hp. Skildril makes a hydraulic post driver that puts out 4.2 hp and 138,000 ft-lbs/min. Seems like the hydraulic hammer should be faster than the drop hammer and more controllable.
Lots of outfits make hydraulic, electric and air jackhammers. The Bosch Brute is electric and generates about 1.5 hp as an example
Next I'll repair the hammer, figure out how to charge it and build a mast with a roller chain hydraulic motor hoist and post holding fixture to keep things straight. I'll also make a larger drive cup attachment to clamp on to this one using a chunk of 1" plate and some proper sized pipe. I'm a little concerned about not having enough weight with the mast but I have a few sections of mainline rail I can strap on to the hammer carrier. As for water well drilling, I'll use the hydraulic post hole auger head, a fluid swivel and centrifugal pump. On the Gulf Coast I used 1" NPT pipe with stops to keep from driving the pins through the couplings. Where I am now I'll need to invest in some rotary shouldered drill pipe. For driving pipe up to 8' long I don't really need a mast but it would be neat. Without a mast for longer pipe all you need to do is weld on a section at a time.
So far I am pleased but disappointed that the hydraulic seals failed so soon and that the nitrogen charge kit is stupid money expensive. At the end of the day I have not built much but instead made what I believe is a successful adaptation.
I guess I've attached these pictures correctly. You can see that my shop helper isn't too work brittle. He just never takes anything seriously.
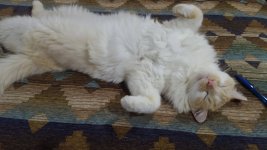
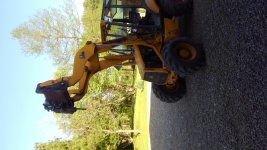
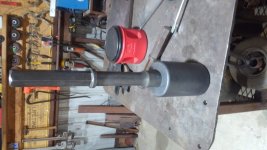
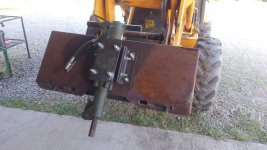