Hey Guys-
I was wondering those of you who have had pole barns built with or have used Perma-Columns in D.I.Y. pole barn build could share how you added shear bracing for the Perma-Column to post connection point.
From my light engineering (no degree) background, obviously a pole barn gets most of it's shear strength from the poles being buried 4' in the ground. When using a Perma-Column you've effectively moved the "moment loading" (I think that's the right term) point to ground level. The pole now acts more like a stud wall where it needs some kind of shear bracing. On a stud wall this is accomplished through the sheathing. Since it is common to add purlins with metal siding with a couple nails between the posts with metal siding screwed to the purlin, you don't get the same shear that you would with common stud framing. As a side note, the wind loading is 90MPH in my building department code book, pole barns dont get inspections though, but I do want to do it right.
My question is, how do you add enough bracing to make the structure sound again? Obviously not looking for an engineering report but some actual builds of things that work. I had though about using "commercial" or "ladder" style purlins in between my posts with the metal screwed through the flats into them. Then the metal acts much more like typical sheathing. Added side benefit of easy insulation and interior wall finishing.
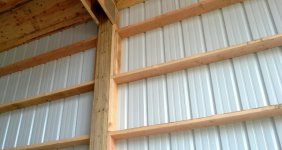
Thoughts? Opinions?
I was wondering those of you who have had pole barns built with or have used Perma-Columns in D.I.Y. pole barn build could share how you added shear bracing for the Perma-Column to post connection point.
From my light engineering (no degree) background, obviously a pole barn gets most of it's shear strength from the poles being buried 4' in the ground. When using a Perma-Column you've effectively moved the "moment loading" (I think that's the right term) point to ground level. The pole now acts more like a stud wall where it needs some kind of shear bracing. On a stud wall this is accomplished through the sheathing. Since it is common to add purlins with metal siding with a couple nails between the posts with metal siding screwed to the purlin, you don't get the same shear that you would with common stud framing. As a side note, the wind loading is 90MPH in my building department code book, pole barns dont get inspections though, but I do want to do it right.
My question is, how do you add enough bracing to make the structure sound again? Obviously not looking for an engineering report but some actual builds of things that work. I had though about using "commercial" or "ladder" style purlins in between my posts with the metal screwed through the flats into them. Then the metal acts much more like typical sheathing. Added side benefit of easy insulation and interior wall finishing.
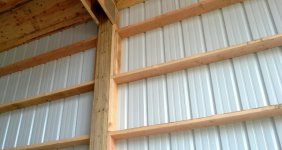
Thoughts? Opinions?