On the same note...it is not a skill with a difficult learning curve...with a modicum of eye-hand coordination the average klutz (m/f) can become quite adequate in a very short time...IMO a very useful skill every DYI'er should possess...
I agree 100% with this. I can solder. Quite well in fact. I do it every day as part of earning a living, it's hard to imagine not being able to. I don't mean this in a rude way to those that can't. I mean once you know how, you realize there are a lot of tasks that are performed better with this knowledge. Let's not forget plumbing. Different heat source, same principle.
BUT, I do remember a time when I couldn't say this. I remember watching someone and they made it look so easy. But I, myself, didn't understand the workings behind it so when I tried I failed. Again and again. It's very frustrating. Especially when your trying to do it under the good of a car. Or, let's say, the dash of a tractor. Like many have suggested, practice on some spare wire, out on a solid surface. Watch some YouTube videos. It really isn't hard once you learn the "tricks". I really don't mean it to brag, only for perspective. For me, doing it every day, that bundle of wires would be about 15 minutes to solder, shrink, tape, and re loom
I don't think words could describe well enough how to do it. YouTube probably has lots of videos where you can see where to apply the heat and how it should flow. Grab one of these to hold your wires while you solder them, it's how i avoid twisting them as mentioned before:
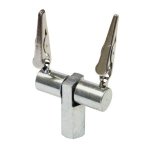
It's an LI55000 from Lisle Tools but I'm sure other companies make them, maybe harbor freight.
The one thing I will say about how I do it that seems to be some different. Rather than twisting or bending, creating fat spots or weak spots to break later. I strip a quarter inch from each wire. Slide on about a 3/4" piece of heat shrink. Dip one of the wires in flux. I straighten the natural twist of the strands of wire so they will "mesh" together. It's kind of a trick to get them to stay just right, hence the tool pictured. Don't leave strands poking out, it's a short waiting to happen. If needed, twist a little after they are meshed together to get them to lay flat. Now apply heat to flow the flux, followed by solder.
Doing it this way with the magnetic tool and my thermostatic solder station to maintain the temp, I pre strip all the wires and each joint takes just a few seconds. The result is a soldered joint stronger than, and nearly as thick as the original insulated wire. The only added thickness is the heat shrink. My customers never can tell where I was