Sodo
Elite Member
- Joined
- Apr 21, 2012
- Messages
- 3,197
- Location
- Cascade Mtns of WA state
- Tractor
- Kubota B-series & Mini Excavator
I need to move this radiator outlet. My plan was to unsolder it, pull ot off, cut a hole and solder it in, then solder a brass cover over the old hole.
I was planning to just use flux & solder from my plumbing kit. I've done lots of plumbing with copper, but never soldered a radiator. I will be paying good attention to avoid melting the long seam between the tank and core.
Any tips?
Where can i get a piece of brass to cover the hole?
Where can I get 'new' outlets? (would like a size 3/8" larger)
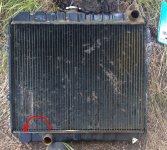
This inlet leaks, you can see the broken solder joint, it had a sealer on it which I peeled off. Is it likely that I can get this clean enough to re-solder?
I was planning to just use flux & solder from my plumbing kit. I've done lots of plumbing with copper, but never soldered a radiator. I will be paying good attention to avoid melting the long seam between the tank and core.
Any tips?
Where can i get a piece of brass to cover the hole?
Where can I get 'new' outlets? (would like a size 3/8" larger)
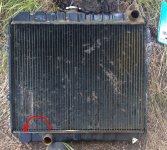
This inlet leaks, you can see the broken solder joint, it had a sealer on it which I peeled off. Is it likely that I can get this clean enough to re-solder?