jrdepew
Silver Member
Yesterday I was at a local hardware store and walked through their welding section. They had a 5lb box of Forney 7018 rods in a box for 16 dollars, which seemed like a decent price. I had been wanting to try 7018, so I picked them up. I got to thinking on the way home that I should post some of my welding on the forum and get some input on what I am doing right/wrong.
Some background first...I started off with a 110V MIG welder years ago and did some welding for car parts and general fixing. Three years ago I bought a house, and a tractor, and right away I started thinking about building/fixing stuff on the tractor, and knew I would need more welder to get it done. I wired the garage for 220 and bought a stick welder with some 6011/6013/E308 rod from a friend of a friend. So far I have just been practicing and made an ugly repair to the skids on a neighbors brush hog.
So, I cut up a piece of 1/4" steel and formed a t-joint, and started laying passes down while taking notes and pictures.
My welder is one of the 230/140A AC/DC welders with the lever on the front to change the current, a very common design from what I hear.
T-joint setup and first pass with 1/8" 6011 at 80A. I was obviously going too fast at the start...probably just excitment. I slowed it down about 2/3rd of the way through and put some decent looking weld down. I read that 6010 may be a bit smoother on DC, but all I have around is 6011 for now. A bit cold and I was moving a bit fast:

Then I ran my first ever 7018 bead...I can tell that I am going to like this rod. Lays down smooth. I forgot to check my welding slide rule for amperage settings for 7018, and although I should have noticed, I ran my first 1/8" 7018 way too cold at 80A (machine was set there from the 6011 pass). The bead looked cold, sounded cold (hindsight after I ran the next beads) and the slag was a pain in the butt to remove:

From there I realized that the 7018 was way too cold, and turned up the welder to 110. Slag removal was easier and I was getting closer to the correct temperature. Some missed spots, probably too cold and too fast still. I noticed that I had a hard time getting the bead to move up into the vertical piece of metal. The overall bead was low and sitting more on the bottom plate, definitely not a 45 degree angle:

120A, this is getting much nicer for sound and slag removal. A little better at melting into the vertical plate, but still to high of a rod angle to get the penetration in the top plate I'm looking for.

Going back to the bottom of the fillet weld, my welds clean up a lot, and I raised the current to 130. Slag removal was much easier and it burned in nicely. This was probably my best bead of the day if I had to guess:
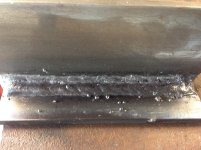
Overall, I had way more weld on the bottom of the T joint that the vertical piece. I need some more practice!! If I keep the rod angle at 45 degrees to the two plates, I seem to keep depositing on the horizontal section, and not getting much weld on the vertical. Should I drop my hand down and reduce the angle to try and push the arc more towards the vertical? Or am I missing something else here? I see some of the fillet welds on here that look very good and they achieve a full 1/4" fillet. Is that with a single pass? Is that possible with 1/8" rod?
More questions, what are the limitations on my machine (other than duty cycle?)...could I weld 1/2" plate with it using multiple passes? Or is 140A not enough and I would have to switch to AC? I have yet to weld anything on AC yet but know I would need to use 6011 and 7018AC if I go that route.
Someone needs to drop one of those PA200's off at my house for me to do a long term test with
.
Long post...let's hear the comments and criticism, I can take it.
Thanks,
Joe
Some background first...I started off with a 110V MIG welder years ago and did some welding for car parts and general fixing. Three years ago I bought a house, and a tractor, and right away I started thinking about building/fixing stuff on the tractor, and knew I would need more welder to get it done. I wired the garage for 220 and bought a stick welder with some 6011/6013/E308 rod from a friend of a friend. So far I have just been practicing and made an ugly repair to the skids on a neighbors brush hog.
So, I cut up a piece of 1/4" steel and formed a t-joint, and started laying passes down while taking notes and pictures.
My welder is one of the 230/140A AC/DC welders with the lever on the front to change the current, a very common design from what I hear.
T-joint setup and first pass with 1/8" 6011 at 80A. I was obviously going too fast at the start...probably just excitment. I slowed it down about 2/3rd of the way through and put some decent looking weld down. I read that 6010 may be a bit smoother on DC, but all I have around is 6011 for now. A bit cold and I was moving a bit fast:

Then I ran my first ever 7018 bead...I can tell that I am going to like this rod. Lays down smooth. I forgot to check my welding slide rule for amperage settings for 7018, and although I should have noticed, I ran my first 1/8" 7018 way too cold at 80A (machine was set there from the 6011 pass). The bead looked cold, sounded cold (hindsight after I ran the next beads) and the slag was a pain in the butt to remove:

From there I realized that the 7018 was way too cold, and turned up the welder to 110. Slag removal was easier and I was getting closer to the correct temperature. Some missed spots, probably too cold and too fast still. I noticed that I had a hard time getting the bead to move up into the vertical piece of metal. The overall bead was low and sitting more on the bottom plate, definitely not a 45 degree angle:

120A, this is getting much nicer for sound and slag removal. A little better at melting into the vertical plate, but still to high of a rod angle to get the penetration in the top plate I'm looking for.

Going back to the bottom of the fillet weld, my welds clean up a lot, and I raised the current to 130. Slag removal was much easier and it burned in nicely. This was probably my best bead of the day if I had to guess:
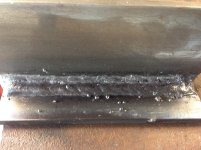
Overall, I had way more weld on the bottom of the T joint that the vertical piece. I need some more practice!! If I keep the rod angle at 45 degrees to the two plates, I seem to keep depositing on the horizontal section, and not getting much weld on the vertical. Should I drop my hand down and reduce the angle to try and push the arc more towards the vertical? Or am I missing something else here? I see some of the fillet welds on here that look very good and they achieve a full 1/4" fillet. Is that with a single pass? Is that possible with 1/8" rod?
More questions, what are the limitations on my machine (other than duty cycle?)...could I weld 1/2" plate with it using multiple passes? Or is 140A not enough and I would have to switch to AC? I have yet to weld anything on AC yet but know I would need to use 6011 and 7018AC if I go that route.
Someone needs to drop one of those PA200's off at my house for me to do a long term test with
Long post...let's hear the comments and criticism, I can take it.
Thanks,
Joe