BufordBoone
Gold Member
I have an old scrape blade that came with the farm. It has a couple of pins for angling and offsetting the blade.
Each pin has a bushing that is welded onto the frame. One bushing was totally loose (I could remove it). The other would wiggle.
Best measurement of the steel is 3/8". I figured, with steel that thick, I should use 1/8" 6011 and run it about 110 to 115 amps. I'll cover that with some 3/32" 7018.
I think I got a good weld but the 6011 sure did lay down a lot of metal. Once I added the 7018, there is even more metal. The weld is not pretty (hope it is strong) but that's OK, I'm learning.
Should I have probably gone with a smaller electrode? I thought about moving the electrode faster but didn't think that would get good penetration. Perhaps I should have cranked the amps up a little more?
Anyway, how do you guys decide what size stick electrode to use?
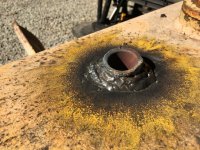
Each pin has a bushing that is welded onto the frame. One bushing was totally loose (I could remove it). The other would wiggle.
Best measurement of the steel is 3/8". I figured, with steel that thick, I should use 1/8" 6011 and run it about 110 to 115 amps. I'll cover that with some 3/32" 7018.
I think I got a good weld but the 6011 sure did lay down a lot of metal. Once I added the 7018, there is even more metal. The weld is not pretty (hope it is strong) but that's OK, I'm learning.
Should I have probably gone with a smaller electrode? I thought about moving the electrode faster but didn't think that would get good penetration. Perhaps I should have cranked the amps up a little more?
Anyway, how do you guys decide what size stick electrode to use?
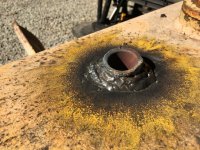
Attachments
Last edited: