Racerwannabe
New member
The hydraulic thumb on my Woods BH75 is complete and in-service! Could not have done it without the outstanding advice from this thread - especially DFKrug and Bumperm. The key was stumbling on a cylinder at Surplus Center that had the right 2.5" bore and exact same retracted length as the existing mechanical linkage. The stroke gave me 1/2" additional extended length than the mechanical linkage, but that didn't hurt me at all. Fairly minor fab which I did myself included the valve mounting plate on the dipper, cutting off and re-orienting the base cross tube on the thumb cylinder to get my ports on the side, cutting DOM spacers for the thumb pin/rod crosstube, and the little aluminum bracket for the valve switch. I'm into it for $325, not including my time or consumables, or replacing a sneaker that I got a bunch of Kubota Orange II overspray on.



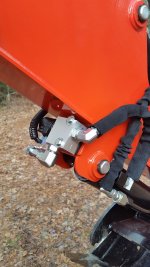
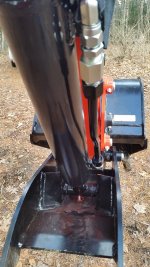
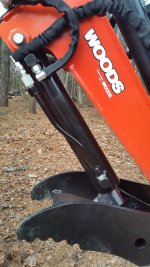
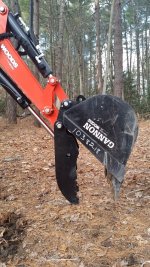

I'm not really happy with the switch install. While perfectly functional, it still looks unfinished. Open to suggestions. The machine tools I used to make the bracket include a drill press, belt sander, Milwaukee Porta-Band, and a Dremel, so I'm pretty limited on what I can do.
One really dumb thing I did was cut the wires that tee off to go up to the switch too short. Only discovered it after I was completely done and testing the wire and hose routing for pinching over the full range of motion of the hoe. When the dipper and boom are fully extended (reaching as far away from the machine as I can with the bucket teeth), the wire up to the switch is uncomfortably strained. If I'm reaching down digging a hole I'll have a problem with that wire. So that's on the list to fix. Also gotta get some dielectric grease on the valve spade connectors. And get some hours on 'er to get all the air worked out. I'm shocked that I have no apparent leaks at any of the fittings, including the hardline compression fittings. I'm hoping that if I don't have any on start-up that I won't have any later (unless I whack something).
Do you guys think the hardline will hold up without being anchored/braced at the base end of my cylinder?



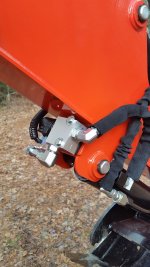
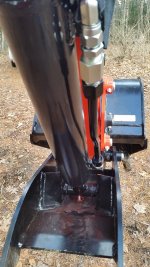
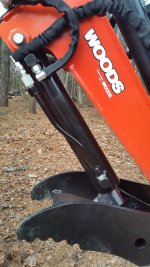
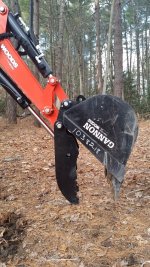

I'm not really happy with the switch install. While perfectly functional, it still looks unfinished. Open to suggestions. The machine tools I used to make the bracket include a drill press, belt sander, Milwaukee Porta-Band, and a Dremel, so I'm pretty limited on what I can do.
One really dumb thing I did was cut the wires that tee off to go up to the switch too short. Only discovered it after I was completely done and testing the wire and hose routing for pinching over the full range of motion of the hoe. When the dipper and boom are fully extended (reaching as far away from the machine as I can with the bucket teeth), the wire up to the switch is uncomfortably strained. If I'm reaching down digging a hole I'll have a problem with that wire. So that's on the list to fix. Also gotta get some dielectric grease on the valve spade connectors. And get some hours on 'er to get all the air worked out. I'm shocked that I have no apparent leaks at any of the fittings, including the hardline compression fittings. I'm hoping that if I don't have any on start-up that I won't have any later (unless I whack something).
Do you guys think the hardline will hold up without being anchored/braced at the base end of my cylinder?