3Ts
Elite Member
Here is my understanding of how this works. The system starts with a pump @ 11 gpm and 2800 psi and is open center. This means that the pump is running when the engine is running and pumping fluid thru the valves and into the tank so nothing is happening which also means the pressure in the system is much less than rated. It follows the red lines to the backhoe valve, then since there are only 2 lines in the backhoe valve (one for pressure) the other has to be the dotted blue line to the tank.
- Why can't the blue dotted line be replaced by the red dotted line as long as the 3PH valve is always centered and not moved? It produces
the same result, the fluid flowing thru the valve to tank.
Now, to actuate a cylinder a valve is moved to block the flow and the valve diverts the flow into the cylinder at one end and provides a "drain" for the other end of the cylinder (we'll leave regen out for now). So, now that the valve has blocked the fluid flow, the downstream pressure falls to zero and the draining fluid continues on down the line thru the centered valves to the tank. Now, if it could be guaranteed that only one valve could ever be activated at a time, only the red lines would be needed. Right? The problem comes when a loader valve and a backhoe valve are activated at the same time. If this happens the fluid from the pump is directed into a cylinder, the fluid from the opposite end of that cylinder instead of meeting zero pressure is then directed into the next cylinder and builds up to system pressure and the fluid from the opposite end of the 2nd cylinder is drained to the tank. If the valves are held in position the overpressure valves will release the pressure downstream, but since the 1st valve directs the flow into a pressurized line then what? Wouldn't the pressure valve on the 2nd bank then release the pressure downstream? Or does the 2nd overpressure valve not protect the input port and only the actuated valves? I don't think I understand why a 3rd line is needed except as a case drain for valve leakage.
My backhoe is a subframe mount and I plan to pull it off and replace it with a set of stack valves to control a hydraulic blade with 4 cylinders. One of the cylinders I will put on this is 2x8 so with 11 gpm the extension time will be less than 2 seconds. I obviously need some sort of metering valve on this. I know about the disk with the 0.03 hole in the fitting and a needle valve to control the flow rate. I've also come across a metered valve as one option in a stack valve that Surplus Center has which appears to do the same thing but at a variable rate. Is there any reason not to use a metered stack valve for all cylinders? Why aren't they always used, their cost is only a few dollars more.
Any thoughts or comments are welcome.
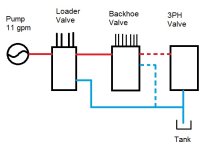
- Why can't the blue dotted line be replaced by the red dotted line as long as the 3PH valve is always centered and not moved? It produces
the same result, the fluid flowing thru the valve to tank.
Now, to actuate a cylinder a valve is moved to block the flow and the valve diverts the flow into the cylinder at one end and provides a "drain" for the other end of the cylinder (we'll leave regen out for now). So, now that the valve has blocked the fluid flow, the downstream pressure falls to zero and the draining fluid continues on down the line thru the centered valves to the tank. Now, if it could be guaranteed that only one valve could ever be activated at a time, only the red lines would be needed. Right? The problem comes when a loader valve and a backhoe valve are activated at the same time. If this happens the fluid from the pump is directed into a cylinder, the fluid from the opposite end of that cylinder instead of meeting zero pressure is then directed into the next cylinder and builds up to system pressure and the fluid from the opposite end of the 2nd cylinder is drained to the tank. If the valves are held in position the overpressure valves will release the pressure downstream, but since the 1st valve directs the flow into a pressurized line then what? Wouldn't the pressure valve on the 2nd bank then release the pressure downstream? Or does the 2nd overpressure valve not protect the input port and only the actuated valves? I don't think I understand why a 3rd line is needed except as a case drain for valve leakage.
My backhoe is a subframe mount and I plan to pull it off and replace it with a set of stack valves to control a hydraulic blade with 4 cylinders. One of the cylinders I will put on this is 2x8 so with 11 gpm the extension time will be less than 2 seconds. I obviously need some sort of metering valve on this. I know about the disk with the 0.03 hole in the fitting and a needle valve to control the flow rate. I've also come across a metered valve as one option in a stack valve that Surplus Center has which appears to do the same thing but at a variable rate. Is there any reason not to use a metered stack valve for all cylinders? Why aren't they always used, their cost is only a few dollars more.
Any thoughts or comments are welcome.
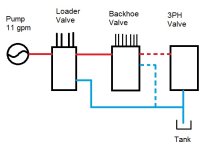