GuglioLS
Veteran Member
- Joined
- Feb 13, 2005
- Messages
- 1,155
- Location
- Edgewood, NM USA
- Tractor
- Jinma 354, 1953 Ford NAA Golden Jubilee, Komatsu Bulldozer
After test fitting the bearings, they were taken off so I could add the swing offset cylinder mount to the boom......
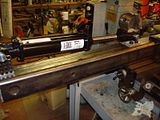
1/2" SHCS were used, the boom is 3/8" thick so they should hold okay. They were bolted on as opposed to welding so in the future as any part wears out, it can easily be replaced.
Larry
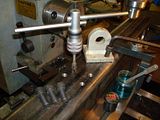
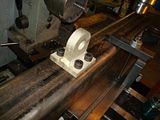

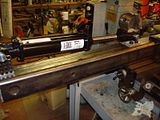
1/2" SHCS were used, the boom is 3/8" thick so they should hold okay. They were bolted on as opposed to welding so in the future as any part wears out, it can easily be replaced.
Larry