GuglioLS
Veteran Member
- Joined
- Feb 13, 2005
- Messages
- 1,155
- Location
- Edgewood, NM USA
- Tractor
- Jinma 354, 1953 Ford NAA Golden Jubilee, Komatsu Bulldozer
MJ-
Oh man that is nice stuff, super tough too. Thanks for all that detailed info and the links. I'll check to see what's available in Albuquerque. I'm a couple weeks off for sure.
When the anvil was a bit more than cherry red, it was immersed in cold water. After that I started to fabricate the Die per Renze's recommendation of 4" wide.
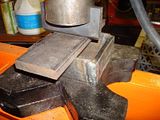
WOW what allot of work to make an Anvil and Die for my hydraulic press. This thing better work or I gonna Kill Renze. In the last pic, the anvil and die are complete and installed onto the press for a trial run with a 1/2" thick x 2.5" wide flat bar............
Larry
Oh man that is nice stuff, super tough too. Thanks for all that detailed info and the links. I'll check to see what's available in Albuquerque. I'm a couple weeks off for sure.
When the anvil was a bit more than cherry red, it was immersed in cold water. After that I started to fabricate the Die per Renze's recommendation of 4" wide.
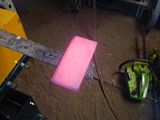
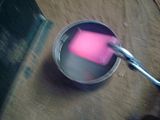
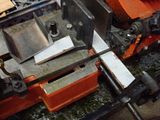
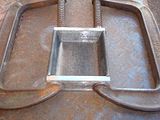
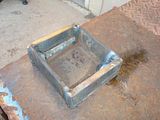
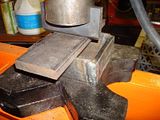
WOW what allot of work to make an Anvil and Die for my hydraulic press. This thing better work or I gonna Kill Renze. In the last pic, the anvil and die are complete and installed onto the press for a trial run with a 1/2" thick x 2.5" wide flat bar............
Larry