Hi kc,
Welcome to TBN! Glad you like the grapple build too.
The material I used is 3/8" thick hot roll plate. The lightening holes were to keep the weight down for my wife's smaller tractor, but if you don't need that, it's certainly not necessary.
Are you going to get a toothbar on that bucket? I would highly recommend you do, because the bucket grapple like this works great with a toothbar. After several hundred hours using bucket grapples on this tractor and my other one, I wish I would've made the jaws long enough so they reach out all the way to the end of the toothbar teeth.
I originally designed these jaws to meet the edge of her bucket without the toothbar on. So what happens is when trying to grab stuff with a horizontal bucket, sometimes the toothbar pushes the object away a little bit and I can't grab it. So I have to make sure I'm under the object enough to grab it that way. I'm talking mostly boulders, bigger rocks and some stumps. Once I get them over the toothbar it's fine. Plus, no problem with shrubs, branches and stuff like that at all. You can see a toothbar would act like a rake or root bucket a little to make it easier to pick up stuff. With that in mind, having the jaws long enough to reach to the end of the toothbar is important.
There is another technique I use to overcome this drawback though. It's the clamshell technique where I raise the bucket up over the object in full dump mode. Then with the grapple wide open, I lower over the object making sure the toothbar tips and the grapple jaw tips touch the ground to swallow up the object into the bucket. I use that technique more for getting smaller plies of brush. Another way I use is to drive up with the bucket horizontal and the toothbar slightly lowered so the tips are even or just under the bottom of the object. Driving into it like trying to pick it. As I do that, I simultaneously start to lift and dump the bucket until it rolls the object with the roll of the bucket. Then set the grapple jaws to capture it. I use that technique more for boulders that tend to roll out of the way or if they are so big that I need the curl power to get it up after I've grabbed it. Both ways work real well, but like I said, a toothbar will make those bucket grapples work wonders.
For example, I took these pictures using my other tractor to show the technique. Here is a small pile that would scoot forward of the tractor if I just dove into it. So clamshelling the pile keeps it from getting away, it crushes it down and allows you get almost all of it neatly and cleanly.
Other stuff you can get easily like Loretta is doing with her tractor.
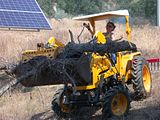