Hi Dave,
You'll see the 332 engine plate down below.
Tonight I did as you said I should not do, and fired up an inductive load. I had previously powered inductive loads with the 3 hp router, and I suppose the welder is a mix of resistive and inductive, and both of those ran fine, but I didn't load the router. So tonight I plugged in my 2 hp air compressor. This isn't a modern compressor where they have fudged the hp ratings. This guy is 30+ years old and is a real 2 hp. I chose this mostly because the compressor was closer to the tractor, easier to plug in and a heavier load on start. The first thing I noted was belt slippage. Then I applied some extra belt tension and the engine slowed down. After a bit, it managed to get the compressor going and from then on it didn't need the additional belt tension, and the engine ran fine cranking out 220 volts from the generator with the compressor finally running. Obviously, I need to go with another increase in pulley size on the generator. The 332 engine on my machine is running at 3220 RPM at full throttle with no load. TractorData.com says that it should be running at 3600 rpm at full throttle. A 6 inch pulley should spin the generator at 3750 if the engine is running at 3220, so this sounds like the next step, and if my torque curve is like the one you posted earlier, then this will be above the peak like we want.
Now I have to find a 6" pulley with a 1" bore.
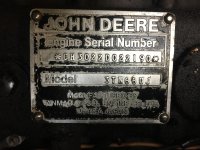
You'll see the 332 engine plate down below.
Tonight I did as you said I should not do, and fired up an inductive load. I had previously powered inductive loads with the 3 hp router, and I suppose the welder is a mix of resistive and inductive, and both of those ran fine, but I didn't load the router. So tonight I plugged in my 2 hp air compressor. This isn't a modern compressor where they have fudged the hp ratings. This guy is 30+ years old and is a real 2 hp. I chose this mostly because the compressor was closer to the tractor, easier to plug in and a heavier load on start. The first thing I noted was belt slippage. Then I applied some extra belt tension and the engine slowed down. After a bit, it managed to get the compressor going and from then on it didn't need the additional belt tension, and the engine ran fine cranking out 220 volts from the generator with the compressor finally running. Obviously, I need to go with another increase in pulley size on the generator. The 332 engine on my machine is running at 3220 RPM at full throttle with no load. TractorData.com says that it should be running at 3600 rpm at full throttle. A 6 inch pulley should spin the generator at 3750 if the engine is running at 3220, so this sounds like the next step, and if my torque curve is like the one you posted earlier, then this will be above the peak like we want.
Now I have to find a 6" pulley with a 1" bore.
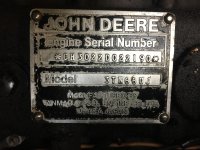