CADplans
Elite Member
Since you are trying to weld thin steel,,, and you have some copper laying around,
why not try putting the copper under the steel as a heat sink.
Although a lot larger, this was the same problem.
I wanted to abrasion resistant weld the edge of some tiller tines.
I clamped some copper under the tiller tine, and stick welded (1/8" rod)
I would avoid trying to weld copper until you master welding steel.
Copper can be VERY tricky to weld, especially if you do not have the machine completely figured out.
why not try putting the copper under the steel as a heat sink.
Although a lot larger, this was the same problem.
I wanted to abrasion resistant weld the edge of some tiller tines.
I clamped some copper under the tiller tine, and stick welded (1/8" rod)
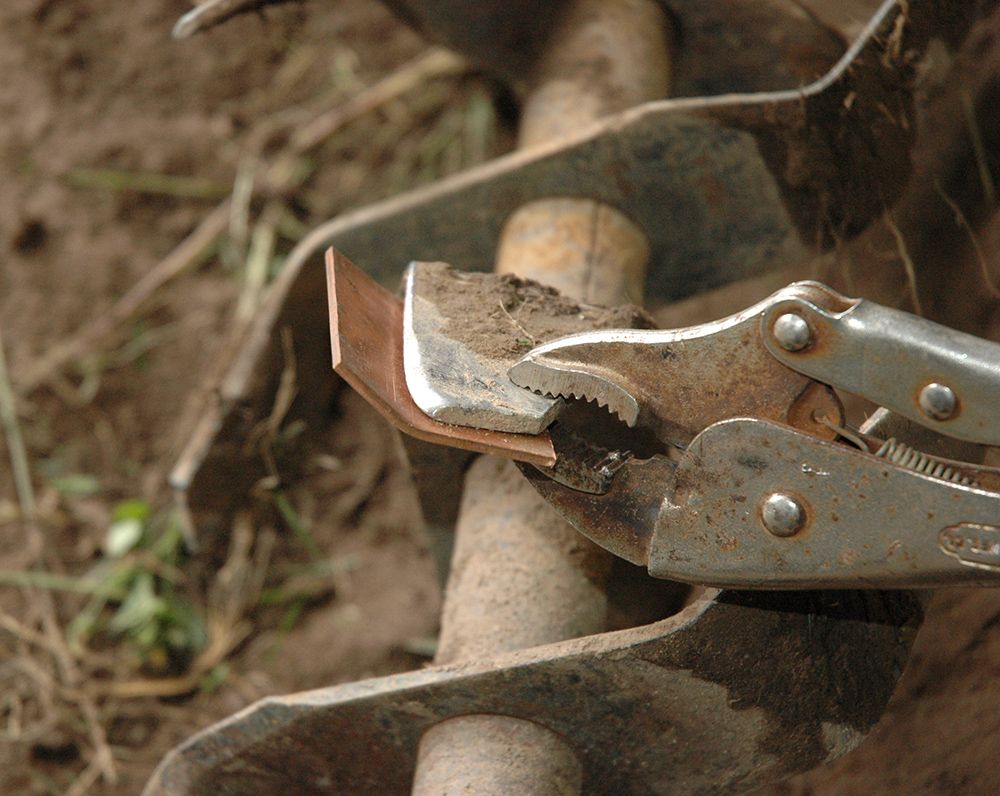
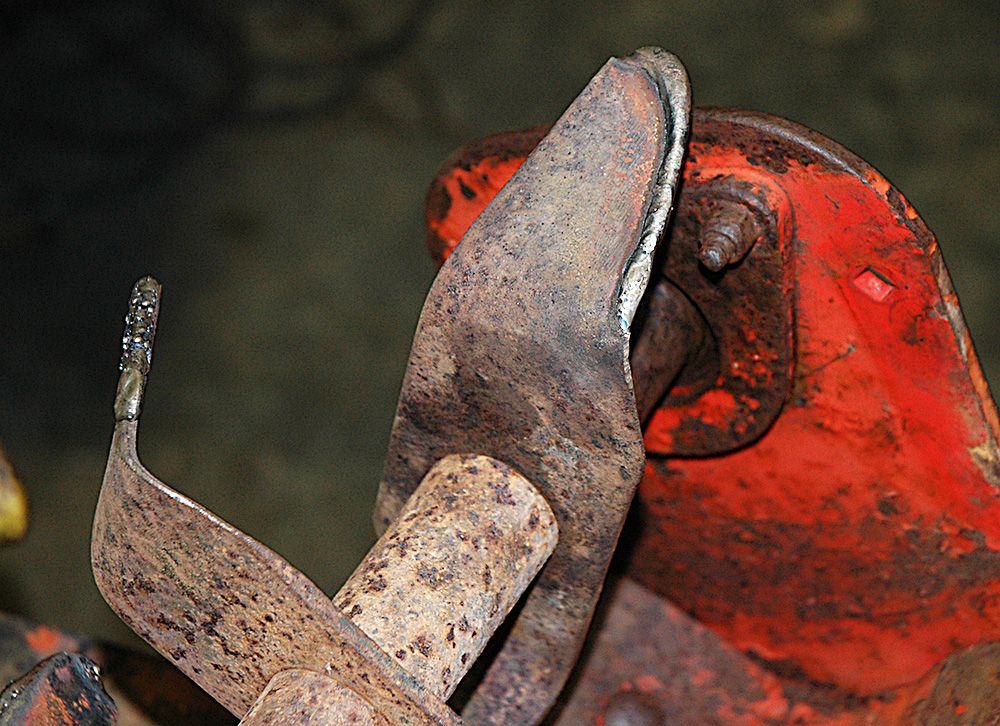
I would avoid trying to weld copper until you master welding steel.
Copper can be VERY tricky to weld, especially if you do not have the machine completely figured out.