CDN Farm Boy
Veteran Member
I got a handful of cash for Christmas and sold a 6.0L motor that I hadn't gotten around to using to buy a plasma cutter from Duncan at Everlast Canada. Still had cash leftover burning a hole in my pocket. With my birthday this past week, added cash from my wife, my folks and my mother-in-law and ordered up enough steel to build a welding table and have a couple chunks left over. Steel was ordered Thurs, delivered Friday and I started cutting today. Shipping slip says 1140 lbs. I'll measure up what is not used to calculate an accurate completed weight but it should be easily north of 900 lbs, closer to the 1000 I figure.
Overall the table will be 4 x 8 with 5' of it 1/2" plate and the other 3' will be cutting slats.
2.5" x .237 wall tubing used for top rails to accept 2" slide in accessories
2.5" x .188 wall legs
2" x .188 used for lower shelf supports
Parts cut and ready for prep and welding:
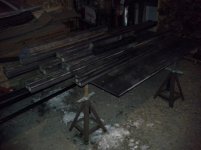
(Sorry for the dark pic)
A question for you experienced welders out there, particularly those that deal with heavy plate like this on a regular basis: How flat should I expect the 4'x5' sheet of 1/2" plate to be?
I figured it would be flat. Not flat like a milled surface but flat to eye with a 4' level. I've got roughly 1/8" gap under the middle of my 4' level when checking the 5' direction. I can pull it flat with a couple big ratchet straps and blocks of 8x8 but don't think that I should have to. I'm concerned that even if I pull it straight before I weld it to the frame, when I take the straps off, it will just return to the bow and pull the frame with it, defeating the purpose of building a flat table.
Overall the table will be 4 x 8 with 5' of it 1/2" plate and the other 3' will be cutting slats.
2.5" x .237 wall tubing used for top rails to accept 2" slide in accessories
2.5" x .188 wall legs
2" x .188 used for lower shelf supports
Parts cut and ready for prep and welding:
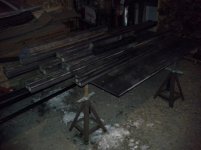
(Sorry for the dark pic)
A question for you experienced welders out there, particularly those that deal with heavy plate like this on a regular basis: How flat should I expect the 4'x5' sheet of 1/2" plate to be?
I figured it would be flat. Not flat like a milled surface but flat to eye with a 4' level. I've got roughly 1/8" gap under the middle of my 4' level when checking the 5' direction. I can pull it flat with a couple big ratchet straps and blocks of 8x8 but don't think that I should have to. I'm concerned that even if I pull it straight before I weld it to the frame, when I take the straps off, it will just return to the bow and pull the frame with it, defeating the purpose of building a flat table.