Second Installment:
I had to repair and rebuild the damaged axle bearing and bull gear before I could move the tractor into the shop. When you are working outside, a guy cannot control conditions and that makes the job even harder. Even though I had gravel as a surface to work on, nothing beats a 7 inch slab of concrete!

Pre-teardown, I got it jacked up and wheel off, now for the real stuff.
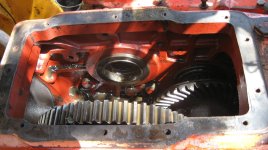
Had to open up the final drive to get at the bull gear. You have to remove the cotter pin then spin off the castle nut and press out the axle, you see the seal is pressed into the housing on the outboard end of the axle and will be ruined when you push it out. The cone race was the only thing left, which is pressed onto the axle journal. When both axles are installed in final drive they have only about a half an inch or less between them so a person can get a flat bar between them and start to pry them out. As they move you have to add additional thin blocks and pry some more, I used some aluminum flat stock for my blocks.
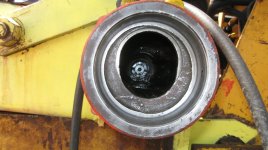
Here you can see the damage caused by the bearing coming apart. The axle was no longer being contained by the bearing, gravity took over dropped the tractor on the axle, which tried to eat all the way into and the top of the housing, however, it had not ground on the all important bearing and seal surface cavity, it looked like it had just started to touch that line. If you look into the axle housing you will see the other axle nut.
By the way; that black hose is my air line draped over the axle housing........
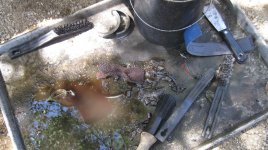
In my clean out pan that I put under the housing you can see what was left of the bearing cage and rollers.........not much.
I had to cut the race to get it out of the axle housing.
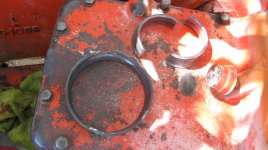
As you can see, this is what is left of both inner and outer races after removal. The larger race has been really cut up by the force of the broken parts. Anybody that has worked on bearings knows how hardened they are compared with mild A36 steel.
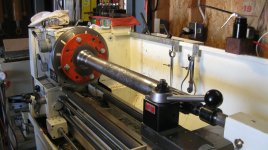
Got the axle on the lathe and all dialed in concentric too. Sounds easy, huh? Try getting something this large, secured and centered to the spindle axis.............. it barely fit between the headstock and the tailstock.
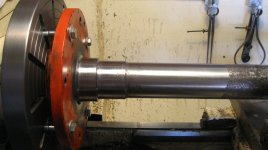
I took off less than a .001 total off of the seal journal but just used emery cloth on the bearing journal and axle. I did not want to reduce bearing surface then I would not have had a press fit if I had changed the diameter.
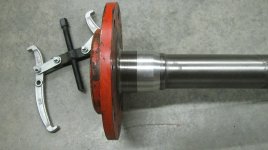
Because the seal goes on the axle before pressing on the bearing cone, I had to machine a taper cuff so as not to damage the seal on that sharp lip. I slid back the cuff to show you how it will work.
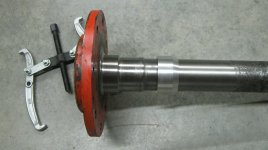
The cuff is now slipped over the bearing journal for final placement of the seal.
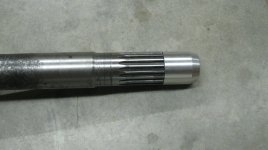
I then had to machine and thread a protective end cap for the end of the axle. When you re-install the axle you have to have this device on or you would ruin the seal that is pressed in the inner housing (there are a total of 2 seals 1 on each end of the axle housing). You will also notice a slight taper about an inch from the spines as the axle goes to a larger diameter. That is inner seal journal. I just cleaned that surface with emery cloth.
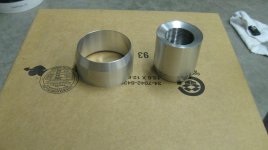
Here are a couple of the tools I had to make to get the axle back in the tractor.
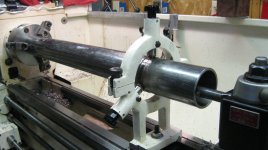
In order to press the bearing cone on the axle I used some DOM (drawn over mandrel) tubing. This is just a long drift tube and slips over the axle to ride on the cone. The interior diameter was just a little under sized to slip over the bearing journal, so once again I had to make anther tool!
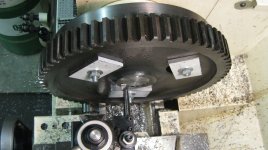
The bull gear was almost too large to mount on my lathe. I turned an inner cone (aluminum) that just tightly fit the lathe plate then turned the opposite end to the matching diameter of the splines of the bull gear. This made it way easier to mate the bull gear to my plate for concentricity.
The reason I went to all that trouble was that the face of the bull gear was ground out badly from the bearing breaking on the other end, when that happened, it allowed the axle shaft to rotate in a conical motion that then chewed up this face. When I removed about .050 to clean up the face, I then had to make a matching shim. You know, I was truly surprised that there was no gear damage from the play at the other end of the axle. I guess there is just enough gear lash that it did not bind up and break corners off the gear, anyway these old hoes are tough!
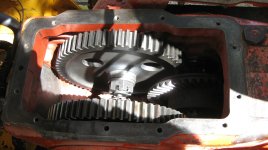
All cleaned up inside gear and axle back in and ready to button up.
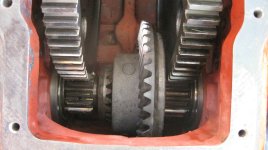
I included this one to illustrate how the ring gear and small spur gears on the stub axles mate up to the bull gears. For those of you that haven not gone into the tractor this far, those stub axles extend through the final drive for the disk and band brakes to attach to. When you do a brake job this is what is on the other end, the spider gears are what allows the other shaft to continue to move while the brake is applied on one side or the other. That makes for a nice turn in tight places.
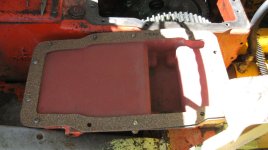
Cap to the final drive, made a new gasket, then re-installed. Time to fill up the housing with gear lube and get the hoe moving toward the shop.