3RRL
Super Member
- Joined
- Oct 20, 2005
- Messages
- 6,931
- Tractor
- 55HP 4WD KAMA 554 and 4 x 4 Jinma 284
I have quite a lot of progress to report today. I started work on the shafts and there are three that need to be made or modified. Each one entailed a lot of work to custom fit them to work in Larry's gear box ... more than the eye meets.
I started on the big worm gear shaft. Larry had given me hollow splines that needed to be connected so they would be long enough to run through the top and bottom of the box. That way he could not only plug in a PTO type shaft into the bottom such as his tilt blade, but also into the top if he wanted. This represented some problems because connecting the two hollow shafts and keeping straight as well as strong and lined up in the center was tricky.
I put the long spline inside the shaft to line them up. Indicated several times in the "V" block.
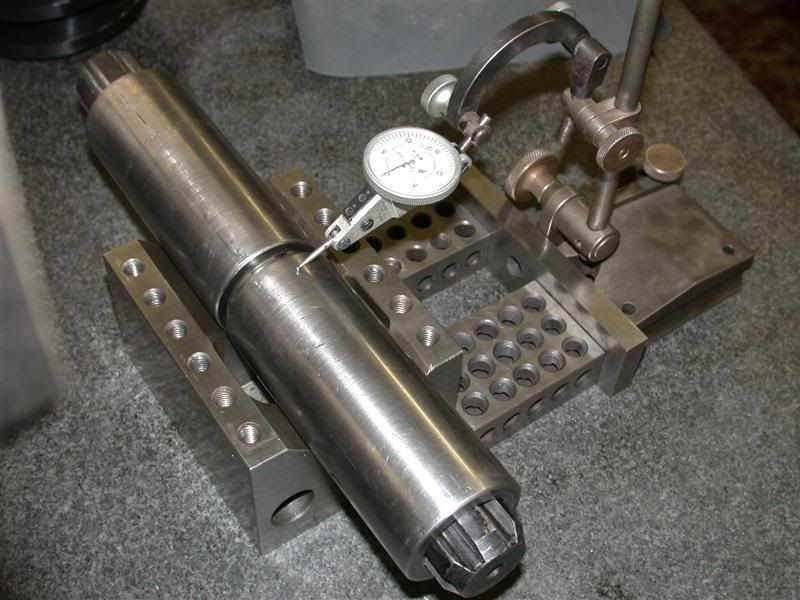
I found the outside did not run true to the inside so I had to position the shaft several times so the OD ran true to the ID. Then I clamped them in position to TIG weld them together. This took several hours to straighten out after welding each time until I was finally able to arc weld the shafts completely.

I started on the big worm gear shaft. Larry had given me hollow splines that needed to be connected so they would be long enough to run through the top and bottom of the box. That way he could not only plug in a PTO type shaft into the bottom such as his tilt blade, but also into the top if he wanted. This represented some problems because connecting the two hollow shafts and keeping straight as well as strong and lined up in the center was tricky.
I put the long spline inside the shaft to line them up. Indicated several times in the "V" block.
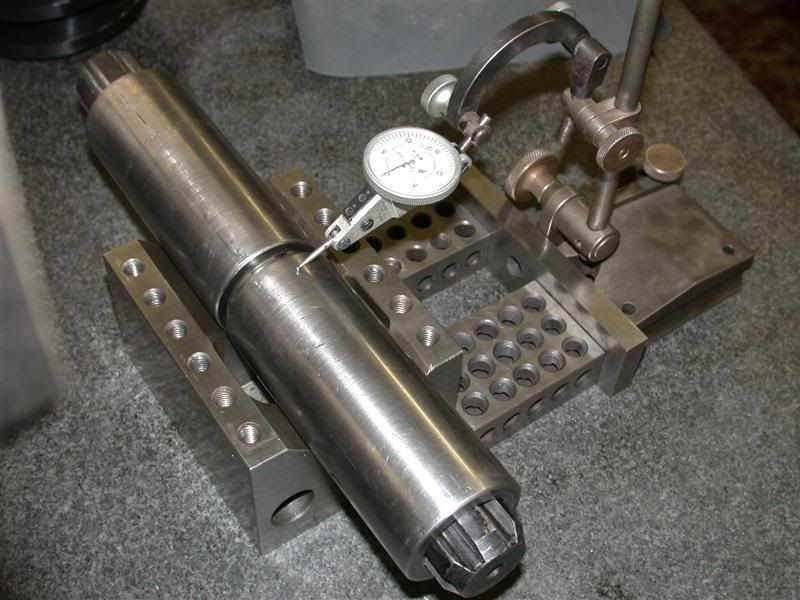
I found the outside did not run true to the inside so I had to position the shaft several times so the OD ran true to the ID. Then I clamped them in position to TIG weld them together. This took several hours to straighten out after welding each time until I was finally able to arc weld the shafts completely.
