GuglioLS
Veteran Member
- Joined
- Feb 13, 2005
- Messages
- 1,155
- Location
- Edgewood, NM USA
- Tractor
- Jinma 354, 1953 Ford NAA Golden Jubilee, Komatsu Bulldozer
This is a closer look of the mount from the other side:
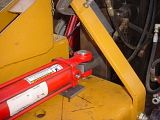
And an overall shot of how far the swing is capable of moving:
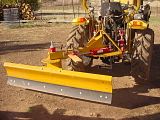
Next is to complete the cylinder mounts (for both ends of the cylinder).
Make a mount for the Gear Box that Rob has completed and add a hydraulic valve to control the swing offset cylinder.
Larry
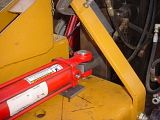
And an overall shot of how far the swing is capable of moving:
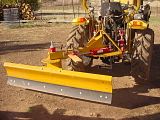
Next is to complete the cylinder mounts (for both ends of the cylinder).
Make a mount for the Gear Box that Rob has completed and add a hydraulic valve to control the swing offset cylinder.
Larry