Titan was all sold of their teeth kits so I bought these>>6 Toothbar Shanks, Teeth, & Pins, For Loader Buckets, 23, 23SP, D5175, TF23D | eBay
Then bought this>> Titan Attachments 72" Custom Toothbar Kit Skid Steer Excavator Kubota Bobcat DIY 498262188 | eBay
Then I put the two together, course the way I do stuff I had do it three times. Since this wasn't a one brand kit, the tooth shanks I thought didn't go back enough on the 1/2"x4" flat bar, so with me and my bright ideas I decided to champfer/tapper the front edge of the flat bar to get the shanks back another 1/2"-ish, I know what a waste of time. So idea mistake No.1, I started to sand and grind the tapper but it was taking to long, mistake 2> I decided to cut the tapper with acetylene torch, it was rough but got it then smooth out the tapper with grinder then laid it on the bucket, clamped down and tacked a shank on each end and called it a night.
Wanted to finish it Sat morning, went out to the shop and happen to look down the length of it on bucket and noticed the bend, cutting the tapper on that flat bar bent the bar 1" in 5', wow couldn't believe that. So since I like straightness the only option was to cut it in 2 places, clamped the crap out of it on top of two angle bars and welded the it back together, back to a straight bar again.
Then clamped back down on bucket, tacked the two bolt-on bars at each end and shanks , mistake 3> I put 1/16 gap on the bolt-on bars at each end, un-clamped the bar for test fit, it went on and off to hard so I cut one shank and bolt-on bar off and shorten another 1/8", put back on with 1/8" spacers on both ends, clamp down and re-tack the bolt-on bar and shank back on, NOW it slides on and off good. So now did the math to spaced out the other 4 shanks and tacked them on flat bar. Then drilled out the holes at each end and bolted together.
Now this I thought might happen, with the flat bar all clamped down and bolted, welded all the shanks, let cool then take off. When it came off the flat bar curled up about 3" from the welding, more then I thought so flipped it over, clamped and heated the flat bar up in two places, got it back down to about 1/2" curl, close enough. Set it back on, put a 1/4" spacer on one end so not to bend bucket, tight it all up. The moral of the story is dont tapper the edge of a 1/2" x4" flat bar with acetylene torch.
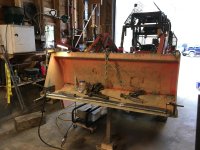
Then bought this>> Titan Attachments 72" Custom Toothbar Kit Skid Steer Excavator Kubota Bobcat DIY 498262188 | eBay
Then I put the two together, course the way I do stuff I had do it three times. Since this wasn't a one brand kit, the tooth shanks I thought didn't go back enough on the 1/2"x4" flat bar, so with me and my bright ideas I decided to champfer/tapper the front edge of the flat bar to get the shanks back another 1/2"-ish, I know what a waste of time. So idea mistake No.1, I started to sand and grind the tapper but it was taking to long, mistake 2> I decided to cut the tapper with acetylene torch, it was rough but got it then smooth out the tapper with grinder then laid it on the bucket, clamped down and tacked a shank on each end and called it a night.
Wanted to finish it Sat morning, went out to the shop and happen to look down the length of it on bucket and noticed the bend, cutting the tapper on that flat bar bent the bar 1" in 5', wow couldn't believe that. So since I like straightness the only option was to cut it in 2 places, clamped the crap out of it on top of two angle bars and welded the it back together, back to a straight bar again.
Then clamped back down on bucket, tacked the two bolt-on bars at each end and shanks , mistake 3> I put 1/16 gap on the bolt-on bars at each end, un-clamped the bar for test fit, it went on and off to hard so I cut one shank and bolt-on bar off and shorten another 1/8", put back on with 1/8" spacers on both ends, clamp down and re-tack the bolt-on bar and shank back on, NOW it slides on and off good. So now did the math to spaced out the other 4 shanks and tacked them on flat bar. Then drilled out the holes at each end and bolted together.
Now this I thought might happen, with the flat bar all clamped down and bolted, welded all the shanks, let cool then take off. When it came off the flat bar curled up about 3" from the welding, more then I thought so flipped it over, clamped and heated the flat bar up in two places, got it back down to about 1/2" curl, close enough. Set it back on, put a 1/4" spacer on one end so not to bend bucket, tight it all up. The moral of the story is dont tapper the edge of a 1/2" x4" flat bar with acetylene torch.
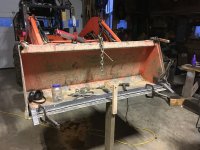
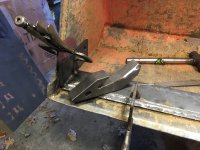
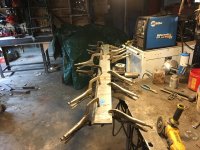
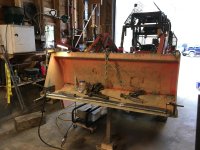