Yup, the Large is the one you want; fits as tight as you can stand it, or looser. Gives you a pretty good range of fitting.
Newer small HF bandsaw -
I give it about a 1.03 - I bought one to make an "off-road" version, spent my usual OCD amount of time building this -
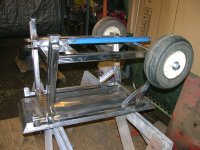
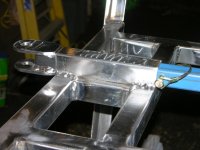
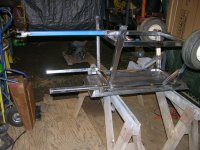
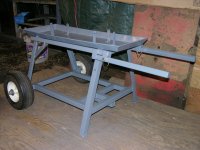
That's when I discovered that my
OLD saw (early '80's) has CAST IRON blade guides and holders, but the
NEW ones are POT METAL. Won't hold a setting, can't get it to cut straight for more than a few cuts if that
Fortunately for me, that chip pan was part of ANOTHER mistake - bought an older saw off CL, foolishly thought the only reason it didn't cut straight was 'cause the PO didn't know how to set one up - but it DID have that chip pan and an actual FRAME of angle under it - the saw itself rapidly turned into a "parts machine" - turned out the thing I
did NOT notice was the crappy welded break in the saw frame 
- so no alignment, but that saw IS OLD ENOUGH not to be pot metal on the blade guides, so hopefully I can swap some parts and get my "off-road" saw going some day...
So, my advice to you is either find an OLD version on CL and make sure you actually watch it cut something, and check the cuts in both dimensions for SQUARE - if it's close and priced right, and (this is REAL important) you check to
make SURE the castings that hold the guide bearings will attract a MAGNET, then it can probably be a good saw. Otherwise, you'd probably have better luck payin' a little more for the Jet version of the 4x6; not sure about Grizzly's version...
You might wanna save this pdf file if you're gonna get ANY one of those saws -
View attachment Basic_blade_adjustment_and_tracking_-_rev-1.pdf
Dry cut - I've pretty much settled on the Evosaw 380, a bit less than other "real" saws in that class, and built pretty solid -
Evolution EVOSAW38 | Evolution Power Tools | Evolution 15
If I get another band saw, it'll most likely be this one
5" x 6" Metal-Cutting Bandsaw w/ Swivel Head | Grizzly Industrial
Definitely more $$, but some of the angles I try to cut (like matching a 2/12 pitch) get REAL tricky, involving removing the movable vise jaw and the angle adj. bolt on main vise jaw, using 3-4 clamps (that won't hit the saw frame when cutting), using a digital angle gauge to set the cut, etc....
Oh, BTW I got a little more done on the HF crane mod - got all welded up EXCEPT for the nuts inside the square tube, need to drill for those FIRST - DID get hole locations punched - used the original I beam end plate for a guide, clamped to MY "sliding clamps", 1/2" transfer punch, 4 whacks per slider, done -
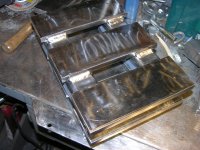
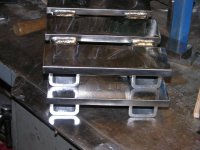
- Sorry for hurtin' yer eyes with those "sloppy HUMAN welds :laughing:
So manana I'll "wake up Maggie, I think I got sumthin' to say to you"

- 8 11/16" holes at ends of those square tubes for 5/8" weld nuts, 4 21/32" holes in the ends of those 3/4" FB lockdown bars, 8 17/32" holes for bolting to the legs (plus opening up the stock holes in vertical post plates to match) then it should be time for degreaser (carb cleaner) and paint... Steve