I tend NOT to talk politics publicly anymore, too many "feelers" instead of "thinkers" - plus, my "sub-trailer trash" neighbors on one side keep me well "prepared" enough to handle anything I have any hope of surviving, including motion sensors, cameras, dogs (including 2 Dobermans that REALLY know the difference between "us" and "them") - you know the old saying; "don't pick on an OLD man - he knows it takes too long to heal, so he'll just KILL ya"...
Somewhat in order -
"either your staying up late or getting up early so what would be the time your time on your post?" - I do tend to stay up kinda late, but not THAT late - you're on East coast time, I'm on West, so if it's 3am on your time it's midnite on mine -
"Are you implying that maggie will be using some sort of cutters instead of drill bits?" - Yup, I have a chuck adapter for the mag drill to use twist drills but haven't used it yet - that'd take another mod to my drilling setup that hasn't happened yet, so any hole I can make with annular cutters gets drilled that way. Cleaner, faster, easier and does NOT WANDER, with or without a punch mark -
"the 6 holes on top was the easiest-ish and would've been if I new about Transfer Punches" - True, and $10 for that HF set I linked isn't too hard to swallow - if those won't work it gets more "spendy" fast -
Punch Sets | MSCDirect.com
"The vertical bottom plate wasn't traceable so that required precise-ish measuring and also required reaming a couple holes."
Maybe - depends on what you have available - They ALSO make things called "Transfer SCREW sets" -
Transfer Screw Sets | MSCDirect.com
If you follow that link, you'll see that you need a
DIFFERENT set for EACH SCREW SIZE - more than a couple sizes needed and you
REALLY start $pending

Plus, most of those screw sets are too LONG to help you on your VERTICAL plate) - but
there's ANOTHER way, if you have access to a metal lathe - I DON'T, but I have a small chuck that fits my mill - here's how -
First, you'd need as many EXTRA BOLTS for that vertical piece as there are holes (6, in this case) - you'd ALSO need at least 2 NUTS in that same thread (like 12mm x 1.25 pitch, or whatever yours are) -
The goal is to end up with 6 short bolts, but with NO HEAD, just a POINT -
So you'd want to use short bolts (more accurate "transfer") - double nuts on the threads, JAM hard together - chuck the NUT in the lathe, turn the OTHER END (where the bolt head WAS) to a point - take the nuts off and repeat with the other 5 bolts.
Now you can screw those "short transfer screws" into the threads on the Kubota - kinda tricky, but you'd need to get ALL of 'em sticking out as close to even as you can -
Next tricky part is to figger a way to hold YOUR VERTICAL PLATE against the points of those screws WITHOUT THE PLATE SHIFTING, til you can tap the plate with a hammer over each "transfer screw" -
Another trick that can help with this - do just ONE punch, like bottom left hole - drill a pilot hole in the plate, not too big - then back THAT "transfer screw" out a bit so it's higher than the rest, the POINT of the screw will then fit into the pilot hole so it doesn't shift - REPEAT this on the TOP RIGHT hole - those two RAISED screw points will keep the plate aligned, so you can tap where the other screws are and mark the rest of the holes...
You'd probably STILL need to go slightly oversize on the holes when drilling, you know how hard it is to get things EXACT -
And yeah, I know it's already DONE - but tricks like these have a way of helping you out of the NEXT jam :thumbsup:
"and I can here you laughing to" - nope, I mostly only laugh WITH people, unless they piss me off :laughing: - otherwise I prefer to help find a SOLUTION (what can I say, age just makes me even MORE wunnerful

)
"so cut apart, do it again, weld it back together on the tractor" - "but this time I tacked two diagonal braces from both ends so it wont fold in, then I rewelded the inside toe bracket, checking squareness as I was welding, then welded the outside top toe brackets. The only way to keep steel from moving is tack on temp braces."
Pretty much, although having all those "high dollar" weld clamps has helped me too - all these "roof frame modules" -
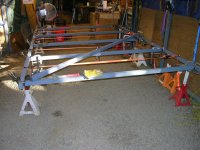
- came out near perfect - note the diagonal brace that's clamped at EVERY CROSS MEMBER - also, with no flat/level surface to fab on, I used one of these
Wixey Digital Angle Gauge with Flip-Out Display | Rockler Woodworking and Hardware
- set up the perimeter pieces on jack stands (with shims for "in-between notches" - Got it level all the way around, then tacked everything, alternating tacks so if one tack would pull left, the next one should pull RIGHT, etc - but the heavy clamps held as good as tacks on that diagonal...
Think that about covers it, guess I better get off my butt and "install some holes" - Oh, speaking of which - another thing I've learned in the last few years is to (if possible) weld EVERYTHING I can FIRST, THEN drill - specially if it's not a good idea to weld close to what I'm adding onto... Steve