3RRL
Super Member
- Joined
- Oct 20, 2005
- Messages
- 6,931
- Tractor
- 55HP 4WD KAMA 554 and 4 x 4 Jinma 284
dtd,
IMO, 1/4" is to skinny. I would use 3/8". Why??
With the added jaws there is a better chance of only one of them hitting and oddball shaped object which places more strain and stress on the whole jaw assembly. It will tweak easier being wider since the force is in the center and the farthest jaw from center seeing resistance will tweak easiest. I would also add more reinforcing between each jaw to tie them together for the same reason. Especially since you are using only one cylinder in the center. I think that is why you see the full width grapples having 2 cylinders. But I like the idea of the wide grapple to suit your needs better.
Please don't be offended, again IMO (my 2¢ worth)...
I don't see having the two end jaws in line with the bucket cylinders as adding strength to the grapple itself, other than that is where you bucket is attached to the fel arms. So the bucket is stronger (backed up by fel arm connection), which in turn makes for a more stable grapple base.
But the grapple strength relies on the manner it is constructed. That is, how well each jaw is connected to each other and the single cylinder mount, the pivots on the bucket, resistance to twisting and tweaking, etc.
I guess what I'm trying to say is although they are all intertwined, failure of the grapple (strength issues such as bending, tweaking etc) is not related to the loader arms.
As an example, I made a thumb for my backhoe. The thumb looks and works like a miniature grapple jaw and was made of 3/8" thick material. The power force points were almost directly in line with each jaw. So I thought with my clever design like that, it would work great and not tweak. It was only 12" wide too.
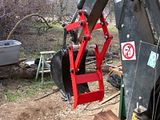
Even designed like that, since I did not have enough bracing in between the two jaws, I still tweaked it and had to reinforce it more. I grabbed an oddball shaped log and one jaw wanted to go farther down than the other...and it did. Just sharing from real experience.
IMO, 1/4" is to skinny. I would use 3/8". Why??
With the added jaws there is a better chance of only one of them hitting and oddball shaped object which places more strain and stress on the whole jaw assembly. It will tweak easier being wider since the force is in the center and the farthest jaw from center seeing resistance will tweak easiest. I would also add more reinforcing between each jaw to tie them together for the same reason. Especially since you are using only one cylinder in the center. I think that is why you see the full width grapples having 2 cylinders. But I like the idea of the wide grapple to suit your needs better.
Please don't be offended, again IMO (my 2¢ worth)...
I don't see having the two end jaws in line with the bucket cylinders as adding strength to the grapple itself, other than that is where you bucket is attached to the fel arms. So the bucket is stronger (backed up by fel arm connection), which in turn makes for a more stable grapple base.
But the grapple strength relies on the manner it is constructed. That is, how well each jaw is connected to each other and the single cylinder mount, the pivots on the bucket, resistance to twisting and tweaking, etc.
I guess what I'm trying to say is although they are all intertwined, failure of the grapple (strength issues such as bending, tweaking etc) is not related to the loader arms.
As an example, I made a thumb for my backhoe. The thumb looks and works like a miniature grapple jaw and was made of 3/8" thick material. The power force points were almost directly in line with each jaw. So I thought with my clever design like that, it would work great and not tweak. It was only 12" wide too.
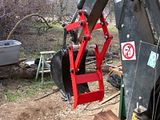
Even designed like that, since I did not have enough bracing in between the two jaws, I still tweaked it and had to reinforce it more. I grabbed an oddball shaped log and one jaw wanted to go farther down than the other...and it did. Just sharing from real experience.