While on the subject, do you want to see some boring details what is involved in making the pins so they can be greased? I thought so.
It takes a little work, but the way I make them allows the Zerk fitting to sit below the surface in a protective pocket to reduce the chance of it getting snapped off. It also gets the grease right between the pin and the bushing. Overkill? Well, whatever floats your boat, right?
Here is the process in detail.
I set up the pin in a "V" block in the mill and centerdrill, drill and counterbore. The drill is the tap drill for a 1/8NPT-27 thread, which is what the Zerk fitting thread is.
Those pins are case hardened, so once you get through the hardened surface, the center is soft enough (about 36RC) to cut and drill with high speed. But be careful when tapping with tapered threads. In order to reduce the chance of breaking a pipe tap, I use a pipe reamer first, then tap for about 7-8 threads engagement. So that's what the end looks like. Ready for the Zerk fitting.
A chamfer makes for nice finished touch.
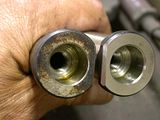