GuglioLS
Veteran Member
- Joined
- Feb 13, 2005
- Messages
- 1,155
- Location
- Edgewood, NM USA
- Tractor
- Jinma 354, 1953 Ford NAA Golden Jubilee, Komatsu Bulldozer
I had a few minutes to burn before my tee time and decided to set up the bottom plate for the pocket milling on it. I positioned it so that I would have enough travel in all directions and then indicated it in square and found center. Here is a video of how to indicate and find center on a large piece.

After indicating it square and parallel to the table axis, use your indicator and pick up the high point at each edge. Use the quill to lower the indicator and move it from side to side and you will see where the high point is as the needle goes to a spot in one direction and then reverses. That spot is the high point so move the dial to zero. Then swing over to the other side and see what that reads. Then split the difference and move the dial again to zero and check both sides until they read the same. Then you are on the dead middle of the piece in that direction. Set your DRO to zero. Then do it for the other direction too and you will be on center. Round pieces are easy as you can sweep around the diameter.
You can also use a depth mic and measure to a pin in the quill and do the same thing. I like using the test indicator for better accuracy.
Here's the first part of the pocket I am milling where the box will sit in and be "trapped" by the steel plate.

Pocket milling has to be exact because if you miss a dimension, you could cut a groove to the outside. So you have to pay attention on this type of machining. You also need to measure frequently because of cutter flex. Your finish pass should be the same depth of cut as the last pass used to measure. This assures you the end mill will cut the same amount off as you have measured. Otherwise it might vary and you'll cut more or less than anticipated.
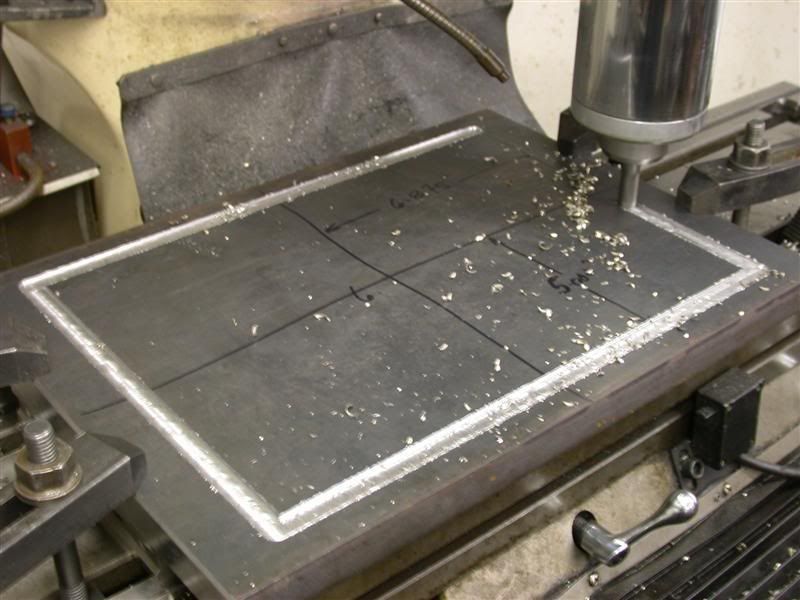
Rob-

After indicating it square and parallel to the table axis, use your indicator and pick up the high point at each edge. Use the quill to lower the indicator and move it from side to side and you will see where the high point is as the needle goes to a spot in one direction and then reverses. That spot is the high point so move the dial to zero. Then swing over to the other side and see what that reads. Then split the difference and move the dial again to zero and check both sides until they read the same. Then you are on the dead middle of the piece in that direction. Set your DRO to zero. Then do it for the other direction too and you will be on center. Round pieces are easy as you can sweep around the diameter.
You can also use a depth mic and measure to a pin in the quill and do the same thing. I like using the test indicator for better accuracy.
Here's the first part of the pocket I am milling where the box will sit in and be "trapped" by the steel plate.

Pocket milling has to be exact because if you miss a dimension, you could cut a groove to the outside. So you have to pay attention on this type of machining. You also need to measure frequently because of cutter flex. Your finish pass should be the same depth of cut as the last pass used to measure. This assures you the end mill will cut the same amount off as you have measured. Otherwise it might vary and you'll cut more or less than anticipated.
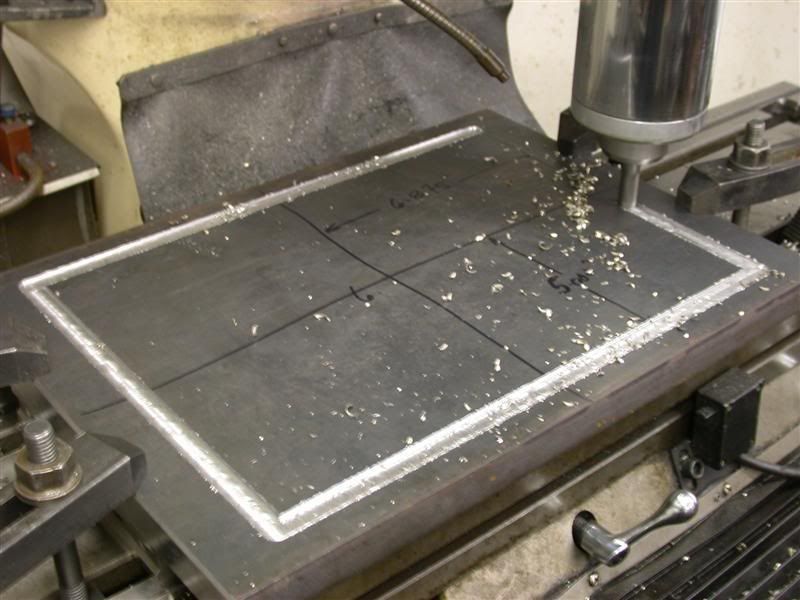
Rob-